L'efficacité n'a jamais été aussi importante pour l'industrie qu'à l'heure actuelle. Cela est particulièrement vrai avec les coûts plus élevés qui placent de nombreuses entreprises et fabricants dans une position concurrentielle désavantageuse.
Alors, comment pouvez-vous maximiser votre productivité et réduire suffisamment les déchets pour rester compétitifs sur le marché mondial ? La réponse réside dans un ensemble de principes et de pratiques collectivement connus sous le nom Lean Management. L'introduction de principes Lean dans ce type d’environnement est l'un des moyens les plus efficaces pour vous aider à améliorer l'efficacité de la maintenance et de réduire les coûts de stocks.
Lean Management et maintenance : stratégie ultime pour améliorer votre productivité
Qu’est-ce que le Lean Management dans le domaine de la maintenance ?
Le Lean Management est une philosophie d’entreprise, plus particulièrement commerciale, visant à optimiser la qualité et l'efficacité de la chaine de valeur en évitant le gaspillage de ressources quel qu’il soit, telles que le temps, l'argent et les efforts. Ce type de gestion ne peut être mis en œuvre avec succès que par un alignement complet basé sur ce principe.
Cette démarche se transpose également à votre service de maintenance. Visant à améliorer le processus de fabrication, ce qui n’est pas forcément le cas de la maintenance traditionnelle, la maintenance dite Lean permet un rôle proactif à vos processus de maintenance. En effet, plutôt que de se concentrer uniquement sur l’entretien et la réparation, elle vous offre la possibilité de vous pencher davantage sur des objectifs et des solutions à long terme.
Un concept provenant de l’industrie automobile
Avez-vous déjà entendu parler du Toyota Production System (TPS) ? Il s’agit d’un système développé par le groupe Toyota, petit constructeur automobile devenu grand, pour organiser ses opérations de fabrication. Son concept de base est la réduction des coûts grâce à l'élimination des déchets et à l'optimisation des capacités de la machine et de l'homme.
Avant ce système, ce géant de l'automobile rencontrait des difficultés telles que des niveaux de stocks déséquilibrés associés à des équipements et des travailleurs excédentaires. Toyota a finalement décidé de miser sur le développement d'un système de production qui peut raccourcir le temps entre le début et l'achèvement d'un processus de production, à savoir de l'entrée des matériaux à l'achèvement du véhicule. Dans ce type de production, seuls les produits nécessaires, au moment opportun, en quantités nécessaires, sont fabriqués. De cette façon, le stock disponible est réduit au minimum.
Il met également l’accent sur :
D'autres entreprises ont rapidement commencé à adopter des méthodologies similaires dans l'espoir d'atteindre le même niveau de succès. Aujourd'hui, la maintenance Lean s’inspire de ses principaux fondements et est largement utilisée par les grandes entreprises du monde entier.
Les caractéristiques de la maintenance Lean
Tous ces termes anglophones peuvent peut-être porter à confusion. Il est pourtant important de les distinguer !
Si nous devions traduire littéralement le terme Lean, il s’agirait de « maigre ». Adapté à un vocabulaire davantage axé sur la production et sur la fabrication, il signifie « éliminer le gaspillage ».
Vous avez peut-être également entendu parler du terme Lean Manufacturing ? C’est un concept similaire, qui fournit un cadre pour guider les opérations de fabrication et de service. Dans la fabrication Lean, les types de gaspillage à surveiller comprennent les temps d'arrêt imprévus, la surproduction, les temps d'attente, les inefficacités de transport et les excédents de stocks.
Comment distinguer maintenance Lean et Lean Manufacturing ?
La maintenance Lean est similaire à la fabrication Lean dans le sens où les deux approches visent à éliminer le gaspillage. Cependant, les déchets peuvent prendre différentes formes lorsqu'on parle de maintenance.
Finalement, quelles sont les principaux fondements de cette stratégie ?
Le Lean management est donc une approche de gestion qui soutient le concept d'amélioration continue et sur le long terme, qui cherche systématiquement à réaliser de petits changements progressifs dans le processus afin d'améliorer l'efficacité et la qualité. En d’autres termes, il aide les entreprises à travailler de manière économique et efficace.
Ces différents gaspillages peuvent se trouver parmi :
- La surproduction
- Les temps d’attente
- Les transports inutiles
- Les étapes inutiles ou sans valeur ajoutée
- Les stocks superflus
- Les mouvements inutiles
- Les erreurs, défauts et rebuts

Pourquoi l’adopter ?
La mise en œuvre de la maintenance Lean offre de nombreux avantages. Parmi eux se trouvent :
- La réduction du gaspillage
On évite de conserver des stocks coûteux plus longtemps que nécessaire.
- La réduction des activités inefficaces
Les activités inefficaces comprennent la recherche d'outils et l'arrêt de l'équipement pour la maintenance sans s'assurer au préalable que les ressources nécessaires à l'entretien sont disponibles.
- L’élimination de l'urgence
Les réparations frénétiques et urgentes sont réduites au strict minimum.
- La réduction des coûts de maintenance
Lorsque l'arrêt des équipements critiques pour la maintenance est bien planifié, cela réduit le temps de production perdu.
De plus, la maintenance Lean se traduit par une productivité améliorée, tout en s'appuyant fortement sur diverses pratiques inhérentes, telles que la maintenance productive totale (TPM), par exemple.
Sans un entretien adéquat, les machines tombent en panne et interrompt le processus de production, ce qui perturbe vos programmes d'entretien et réduit la durée de vie de votre équipement. La maintenance Lean vous aide donc à effectuer plus de travaux de maintenance efficaces avec moins de ressources.
Grâce à la mise en œuvre de cette approche, vous devez identifier et éliminer les actions qui gaspillent vos ressources internes, améliorer les processus inefficaces et accélérer vos interventions de maintenance d’urgence.
Le résultat final ? Un processus de maintenance rationalisé et une réduction significative du coût global de maintenance, tout en offrant un service égal ou supérieur.
De quoi avez-vous besoin pour développer cette méthode ?
En réalité, la maintenance Lean doit être vue davantage comme un outil qui peut faire ses preuves dans différentes situations et qui s’inspire de diverses stratégies.
Une maintenance proactive déjà mise en place
La base. Dans la maintenance Lean, des mesures proactives sont prises pour prévenir les pannes d'équipements grâce à des actions de maintenance prédictive et préventive. L'objectif est d'éliminer les travaux de réparation en prévenant les pannes d'équipement.
> GMAO en maintenance industrielle : 3 types de maintenance
La maintenance productive totale (TPM)
La TPM est une stratégie d’amélioration de l’équipement à l’échelle de l’organisation, qui s’appuie sur une philosophie comprenant 8 piliers, qui lui permet d’atteindre un niveau élevé de performance industrielle. De plus, chaque membre de l’organisation a un rôle proactif à jouer pour contribuer à cette quête d’efficacité et de qualité.
L’objectif de la TPM ? Zéro panne d’équipement. Même si cet objectif peut sembler inaccessible, il s’agit surtout d’identifier et d’éliminer les causes des pannes. Cette méthode met l’accent sur une culture d’entreprise animée par un état d’esprit évolutif afin d'améliorer durablement la productivité au sein de la production.
La maintenance productive totale engage chaque membre de votre organisation pour minimiser tous types de pertes car elle se concentre sur différentes cibles :
Cette stratégie vous aide à détecter, exposer et éliminer tous défauts mineurs des équipements, à établir et maintenir des conditions basiques pour ces derniers, à identifier et instaurer des conditions de fonctionnement optimales et à corriger chaque défaillance identifiée.
La philosophie des 5 S
La méthodologie organisationnelle des 5S est intrinsèquement liée à la maintenance productive totale.
L'objectif de la méthode 5S est d'organiser et de concevoir efficacement votre propre lieu de travail afin que tout ait une place fixe. Cette méthode est un processus systématique qui vise à améliorer l'organisation du lieu de travail pour les employés.
Un lieu de travail bien rangé est la condition préalable à un travail de haute qualité. Idéalement, cela se traduira par moins de retards, de gaspillage ou d'accidents du travail. La méthode 5S se compose au total de cinq étapes.
A l'origine, les cinq "S" sont dérivés des termes japonais :
- Seiri = trier
- Seiton = Classer, ordonner
- Seiso = Nettoyer, dépoussiérer
- Seiketsu = Standardiser
- Shitsuke = Formaliser
Ce système permet ainsi de réduire les déchets et d'optimiser la productivité en maintenant un lieu de travail ordonné.
La méthode Kaizen
Le concept de kaizen, interprété comme « amélioration continue », est construit autour de petites améliorations continues qui s'ajoutent à des changements significatifs au fil du temps, par lesquels une organisation peut améliorer ses processus.
Contrairement à la fabrication Lean, qui est une méthode qui améliore des aspects spécifiques d'un produit ou d'une opération, l'approche kaizen est une philosophie qui vise à réduire les déchets, à réaliser une amélioration continue et à améliorer la qualité dans son ensemble.
Il y a toujours de la place pour l’amélioration, telle est la philosophie de Kaizen. Ce qui signifie que la culture de l'organisation doit être constamment axée sur la recherche de processus qui peuvent être rendus plus efficaces ou efficients. Cette responsabilité incombe à tout le monde, pas seulement aux managers ou aux cadres.
Inventaire MRO
L'inventaire MRO fait référence aux fournitures, pièces de rechange et autres matériaux nécessaires à l'entretien, à la réparation et aux opérations de routine (ou MRO). Cet inventaire est essentiel au bon fonctionnement d'une entreprise.
Cependant, contrairement aux matières premières, ce stock ne fait pas partie des produits finis proposés aux clients. Les fournitures de bureau, les produits de nettoyage, les outils de réparation, les équipements de protection individuelle et les équipements de sécurité sont quelques exemples d'inventaire MRO.
En raison de sa faible part dans le coût global, les entreprises - les petites entreprises en particulier - ont tendance à négliger les coûts d'inventaire MRO uniquement pour voir une augmentation inattendue de leurs frais généraux plus tard.
Un logiciel de gestion de maintenance (GMAO) : un « must-have » pour vous accompagner dans cette démarche
L'un des meilleurs moyens pour convaincre ses équipes à tendre vers le changement et d’adopter de nouveaux processus est probablement d’en faciliter la transition. Pour la rendre aussi fluide que possible et assurer une utilisation continue, pourquoi ne pas vous tourner vers un système de GMAO ?
Cet outil entièrement personnalisable peut faciliter le suivi des changements positifs et fournir la visibilité nécessaire pour accéder, créer et partager facilement des rapports d'avancement à l'aide des données.
Il est par ailleurs important d'utiliser un logiciel qui motive vos employés dans leurs efforts continus pour assurer le bon fonctionnement de votre organisation. De la planification de la maintenance préventive au suivi de l'utilisation des pièces, une GMAO organisée peut simplifier les processus.
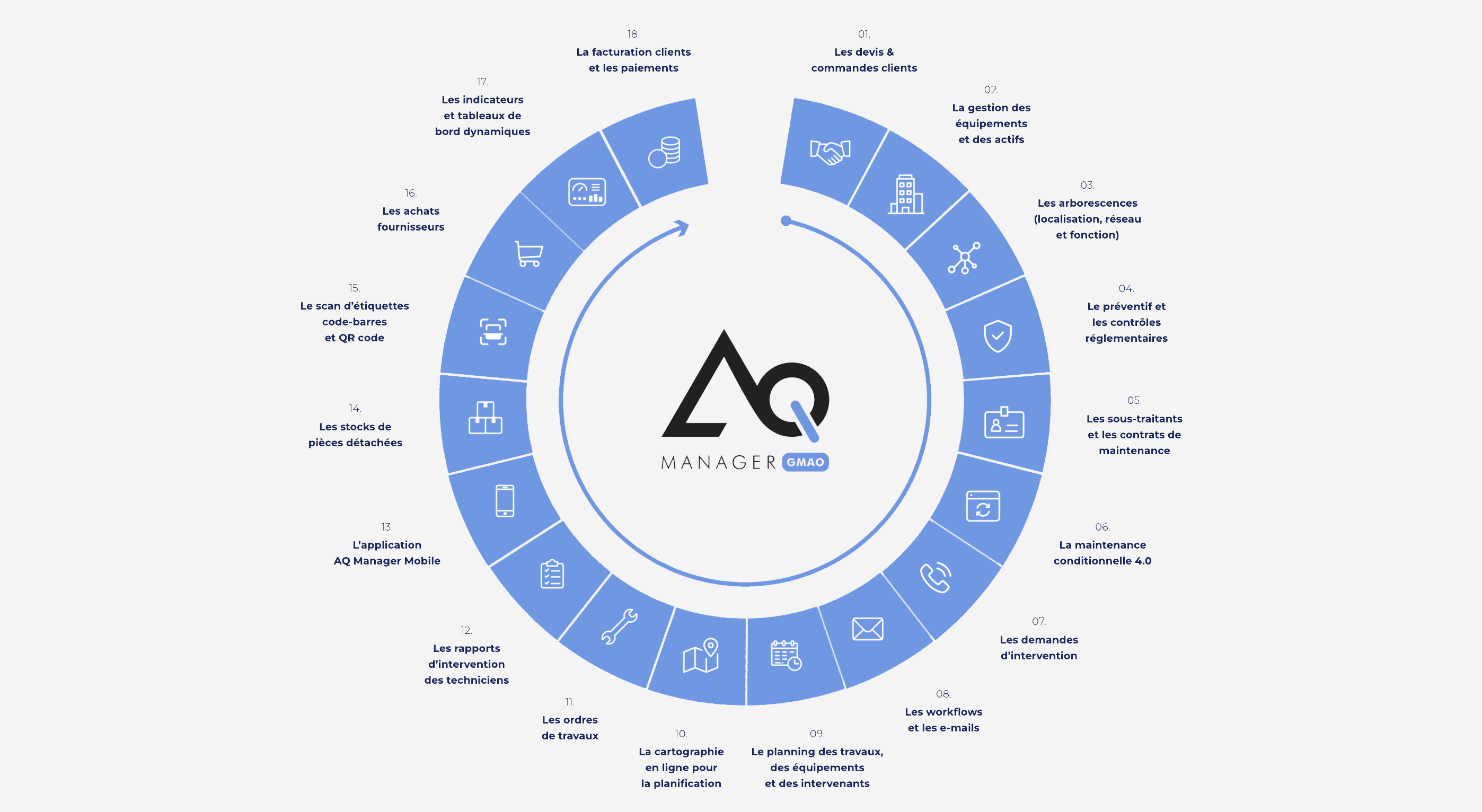
Ce type de progiciel assiste le processus de maintenance Lean en gardant les employés responsables du travail, en s'assurant que le travail est effectué correctement et à temps, et en conservant un historique précis du travail effectué, des mesures prises et des pièces utilisées.
Si des actifs ou des équipements tombent en panne, les processus pour les réparer, y compris les routines de maintenance préventive, peuvent être facilement atteints et potentiellement améliorés.
Un système informatisé de gestion de la maintenance est donc le strict minimum pour améliorer l'efficacité dans tous les domaines, de la gestion des ordres de travaux à la planification globale, en passant par la planification de la maintenance, la gestion des pièces de rechange, la gestion des techniciens mais aussi :
Le tableau de bord dynamique pour suivre les tendances et les dérives
Avec une fonctionnalité intégrant des tableaux de bord dynamiques, vous avez la possibilité de suivre les tendances et d’accéder aux données en temps réel (telles que les différents KPI). Augmentez l'efficacité, réduisez les coûts de main-d'œuvre et réduisez les temps d'arrêt grâce à un tableau de bord dynamique.
Trouvez le problème avant qu'il n’en devienne un, grâce aux données historiques. Ces dernières permettent d'examiner les pannes, leurs causes et les réparations (arbre de diagnostic de pannes) et représentent donc un véritable catalyseur pour analyser les actifs et obtenir un grand nombre d’informations.
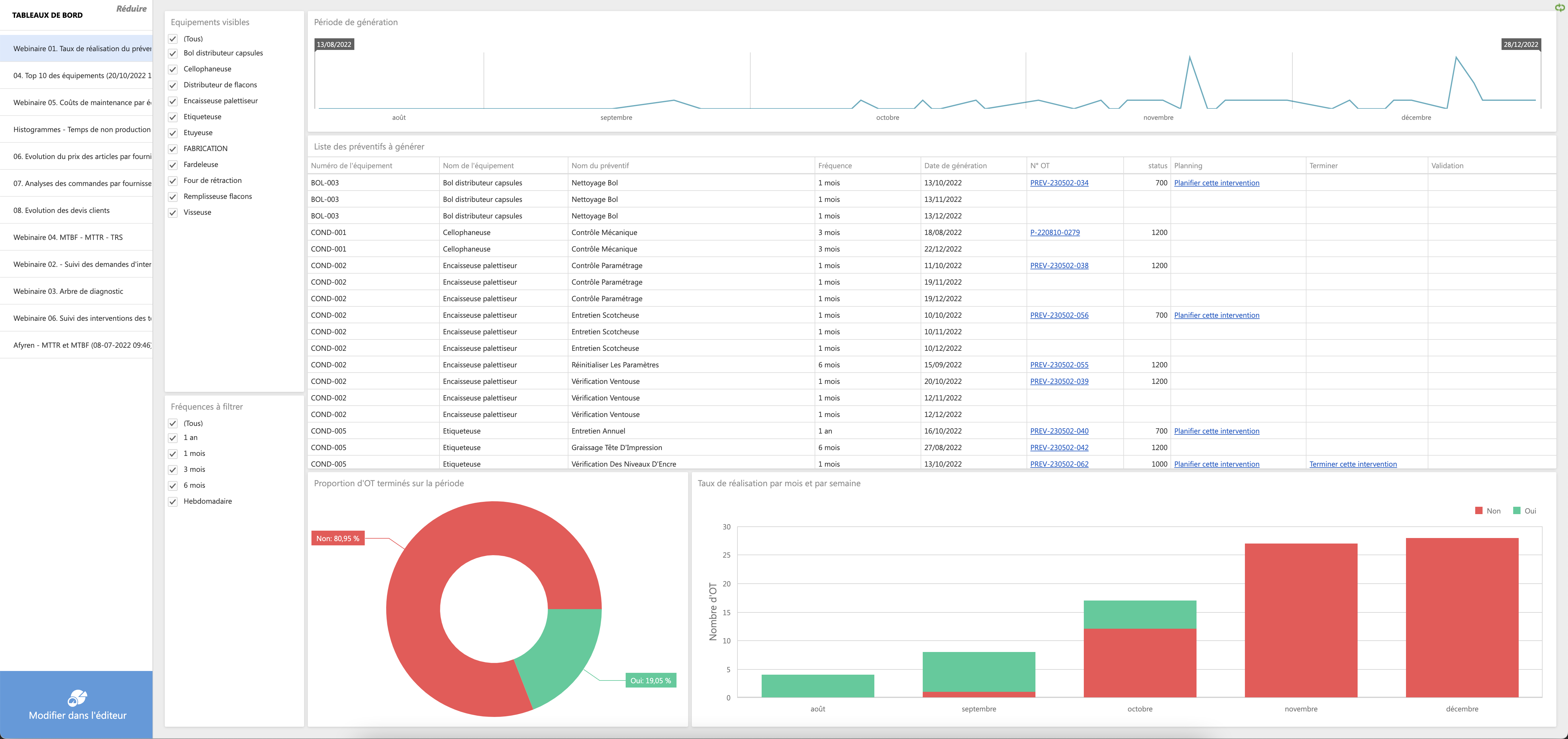
> KPI maintenance industrielle : quels indicateurs pour un directeur ?
Les entreprises qui utilisent la maintenance Lean répondent aux exigences de la fabrication et de la production, et constatent généralement une augmentation de la qualité de leurs produits ou services, ce qui peut profiter à la fois à la culture d'entreprise et au résultat net. Cette stratégie, combinée à un logiciel tel qu’AQ Manager GMAO, crée une véritable dynamique de maintenance proactive.
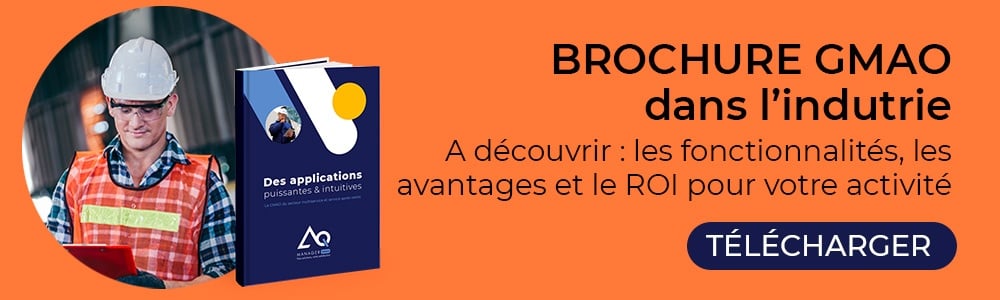