Toute personne étant dans le secteur de la maintenance sait à quel point les pannes et défaillances peuvent avoir un impact sur la production toute entière. C’est par ailleurs l'un des risques que les acteurs du secteur industriel redoutent probablement le plus.
Avec le rythme effréné et la diversité des tâches qui composent votre quotidien de responsable ou de technicien de maintenance, une stratégie bien établie semble être votre meilleur atout pour limiter les pertes et mener à bien votre production. Et la GMAO, un allier de taille…
Diagnostic de panne : l’importance de limiter la casse machine
Les pannes et les temps d'arrêt imprévus représentent de grandes menaces pour atteindre vos objectifs de production. Lorsqu’un équipement de fabrication tombe soudainement en panne, beaucoup de choses se dérèglent.
Un effet boule de neige se produit : une panne survient, la productivité s'arrête alors immédiatement. La pente peut être raide et la descente rapide, les revenus baissent inévitablement, les techniciens sont sous pression et les clients, quant à eux, sont déçus en raison du retard de livraison. Selon la gravité de la situation, les conséquences atteignent chaque recoin de votre organisation.
Vous connaissez probablement l’adage : mieux vaut prévenir que guérir. C'est pourquoi vous devez être assurés que chaque machine fonctionne au mieux de ses capacités.
Déterminer les causes des défaillances pour prévenir la perte de productivité
Lorsqu'une machine tombe en panne, cela coûte inévitablement à votre entreprise des ressources, du temps et de l'argent. Malheureusement, cela peut être le cas pour de nombreuses raisons : un plan de maintenance inapproprié, une documentation incorrecte, une mauvaise tenue de registres et l'exécution de la maintenance aux intervalles trop éparpillées…
Que la panne soit erratique (inattendue, sans signes avant-coureurs), intermittente ou progressive, il est d'abord important de comprendre de quoi il s'agit et pourquoi cela se produit afin de l’anticiper et de la prévenir.
-
Les accidents et les erreurs des opérateurs
Travailler dans l’industrie manufacturière représente un risque quotidien, notamment en raison de la machinerie lourde, des pièces, des substances et produits chimiques nocifs, etc. Une pièce manipulée ou utilisée de manière incorrecte peut endommager les composants internes et provoquer une panne.
La chute d'un équipement peut également entraîner l’endommagement de celui-ci, ce qui peut entrainer son arrêt de fonctionnement.
> GMAO et maintenance préventive industrielle pour assurer la sécurité
L'entretien peut sembler une évidence. Passer à côté de la maintenance courante de vos équipements industriels est risqué. Si un entretien de routine est inadéquat, l’équipement ne peut fonctionner à pleine capacité, finit par tomber en panne et entrainer une inefficacité et des coûts inévitables.
-
L’obsolescence des machines
La détérioration naturelle des machines dans l'industrie manufacturière peut soulever des problèmes à tous les niveaux. Non seulement les pièces de rechange peuvent avoir un coût élevé (notamment pour les anciens modèles), mais les réparations peuvent également être coûteuses et prendre du temps. Les risques sont larges dans le cadre d'un fonctionnement dans un environnement de fabrication sans interruption ou accidents.
-
La défaillance d’une pièce de roulement
Une défaillance de roulement, souvent causée par un défaut d’alignement, un desserrage, un frottement etc., est une raison commune aux pannes et défaillances prématurées. Dans la mesure où les roulements sont souvent les composants les plus fréquemment présents d’une machine, une défaillance peut entraîner des arrêts imprévus coûteux, des dommages aux pièces adjacentes et des coûts de réparation significatifs.
-
Le manque de formation des techniciens
Les erreurs des techniciens représentent des causes vitales de défaillance et de panne des équipements. Les humains ne sont pas des machines et sont enclins à faire quelques erreurs ici et là. L'oubli, la fatigue et le manque de formation peuvent, par exemple, être les principaux responsables de ces erreurs.

Comment remédier aux pannes de maintenance industrielle ?
Le diagnostic de panne pour identifier les opportunités d’optimisation
Le diagnostic de panne fait partie des fondements de la maintenance industrielle. Il s’agit plus particulièrement du processus d'identification des pannes des composants et des systèmes défectueux. La détection et le diagnostic jouent un rôle décisif dans l'optimisation des processus de maintenance et du cycle de vie des équipements.
Son objectif est donc d’optimiser les coûts de maintenance tout en améliorant la fiabilité, la disponibilité, la maintenabilité et la sécurité des machines.
Le diagnostic de panne commence par la reconnaissance des symptômes et suit généralement une approche systématique en plusieurs étapes :
- Identifier le problème, détecter le défaut
- Rechercher une solution,
- Tester cette solution, et
- Résoudre le problème.
En outre, cette stratégie fonctionne en surveillant et en analysant en permanence les données en temps réel de l'état des équipements et en détectant le moindre problème. Les données recueillies sont ensuite traitées informatiquement pour produire des alertes et permettre une intervention de maintenance.
Les technologies émergentes permettent par ailleurs un traitement plus rapide des données. La détection traditionnelle des pannes a évolué vers des systèmes de gestion de maintenance (GMAO) qui non seulement détectent celles-ci, mais identifient également la cause première et mettent en œuvre des actions concrètes et correctives pour éviter qu'elles ne se reproduisent.
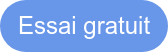
Être proactif (et non réactif) avec une GMAO moderne
Votre organisation possède probablement de nombreux actifs qui doivent être inspectés régulièrement par la maintenance. Faire cette tâche manuellement laisse beaucoup de place à l'erreur humaine. Investir dans le bon logiciel de gestion de la maintenance peut donc vous aider à automatiser les routines d'inspection avec moins de paperasse.
Voici ci-dessous nos conseils pour gérer et prévenir les pannes de vos équipements, et comment tirer vos épingles du jeu grâce à une solution logicielle de gestion de maintenance.
-
Effectuer la maintenance préventive
La maintenance préventive doit être considérée comme étant la santé des équipements de fabrication. Son importance dans le secteur industriel ne peut être négligée car elle joue un rôle vital dans l'efficacité de votre organisation.
Cette stratégie proactive convient parfaitement aux actifs critiques et coûteux et implique de programmer et d'effectuer l'entretien de la machine en fonction d'intervalles basés sur leur utilisation.
La réalisation d'inspections régulières et approfondies des actifs est par ailleurs un moyen très efficace d'identifier rapidement les problèmes. Trouver le bon calendrier de maintenance vous aide à passer au crible les problèmes et à les identifier à la source. C’est pourquoi un logiciel de gestion de maintenance moderne est doté de « calendriers » qui fonctionnent pour vos équipes, pour vous aider à planifier les interventions, organiser les actions nécessaires et ainsi anticiper les dysfonctionnements.
-
Maintenir de bons enregistrements et historiques des entretiens
Le contexte est essentiel lors d’un dépannage et l'historique d'entretien joue un rôle essentiel dans la mise en œuvre d'une stratégie de gestion de maintenance et de stocks réussie.
Si un technicien a facilement accès aux ordres de travaux, aux inspections et à l’historique associé à un équipement, il est plus facile de réduire la liste des causes possibles de la panne.
L'utilisation d'un logiciel pour documenter les événements de maintenance vous permet de concevoir des stratégies et plus important encore, l'historique de maintenance d’un outil de GMAO permet aux techniciens de suivre les tendances des problèmes rencontrés sur les modèles d'équipement et les pièces. L'utilisation de ces informations pour fournir des analyses perspicaces aide finalement à réduire les cas de défaillance.
Cela vous fournit également une capacité à visualiser l'état en temps réel des actifs critiques sur tous les sites de votre entreprise, ce qui peut avoir un effet positif sur le plan financier de vos activités.
La traçabilité est également importante pour une bonne gestion des risques. En effet, l’outil de gestion de maintenance est capable de tracer les opérations de maintenance déjà réalisées. Grâce à cette fonctionnalité, le responsable peut ainsi intégrer des travaux de maintenance supplémentaires si nécessaire.
-
Suivre les bons indicateurs grâce au tableau de bord dynamique
En tant que responsable, un certain nombre d’indicateurs vous sont particulièrement utiles quotidiennement. En effet, les mesurer vous aide à réduire les pannes, la maintenance excessive et optimiser les tâches de vos équipes.
Un générateur de tableaux de bord dynamiques, intégré à un outil de gestion de maintenance, vous offre une visualisation de tous types de statistiques, d’indicateurs pré-paramétrés et de KPI personnalisés. Ce type de module contribue ainsi à repérer les tendances les plus notables et finalement, d’améliorer l’efficacité de votre service de maintenance.
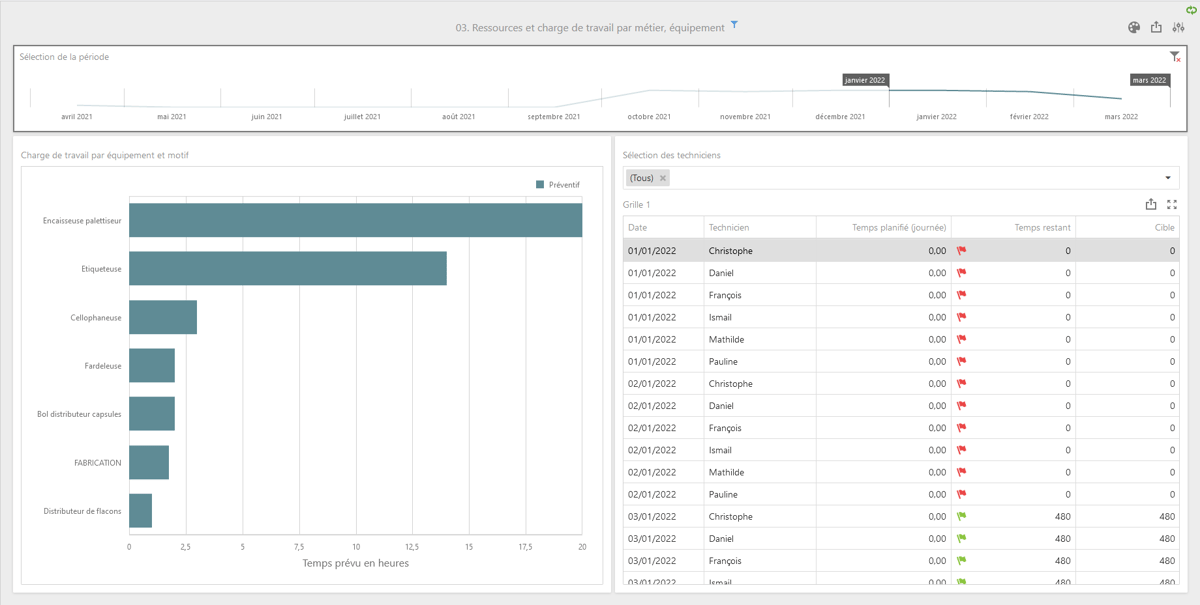
Nous le savons, les incidents techniques ont de réelles conséquences pour une entreprise. C’est pourquoi, il est capital de quantifier les mesures relatives aux temps d’arrêt et à l’efficacité à laquelle les problèmes sont résolus. Deux indicateurs sont couramment utilisés en industrie : le MTBF (Main Time Between Failure) et le MTTR (Main Time To Repair).
Le MTBF, dans un premier temps, représente le temps moyen écoulé entre les pannes et est la mesure de base pour la fiabilité d’une machine. Son augmentation démontre une amélioration de la qualité de vos processus de maintenance.
Temps de fonctionnement total sur une période donnée
___________________________________
Nombre de pannes
Ensuite, le MTTR est le temps nécessaire pour exécuter la réparation d’un équipement. Cette métrique indique davantage l’efficacité des actions qui vont être menées pour corriger le processus. Contrairement à l’indicateur précédent, il est important qu’il soit réduit au maximum pour éviter une perte de productivité en cas d’indisponibilité de l’équipement.
Nombre total de maintenance
_____________________________________________
Nombre total d'actions de maintenance sur une période donnée
-
Valider et documenter la solution
La bonne information est essentielle lorsqu'il s'agit de faire face à une panne. Promouvoir une culture de documentation approfondie et de transparence, ainsi que son partage au sein de l’organisation, est le meilleur moyen de minimiser les délais de maintenance et de maintenir le fonctionnement des machines dans des conditions optimales.
Il est important de prendre de bonnes notes lorsqu'une pièce tombe en panne de façon inattendue. Ces informations partagées avec les différents services fourniront un aperçu de l’état de fonctionnement de l'équipement. Les notes, quant à elles, sont attachées directement dans la fiche de l'équipement, garantissant que rien ne se perd.
-
Former les techniciens de maintenance de manière adéquate
Le milieu industriel est connu pour être un milieu hostile. L’exposition aux produits chimiques, à des équipements à température élevée ou dangereux, aux diverses défaillances de ceux-ci… nombreux sont les risques auxquels sont exposés les techniciens.
C’est pourquoi la formation en sécurité industrielle est extrêmement cruciale pour le succès de tout fabricant car elle garantit que tous les équipements de l'usine, qu'ils soient neufs ou anciens, fonctionnent en toute sécurité, efficacement et pour un rendement maximal.
Gestion numérique des pannes : adoptez une solution mobile
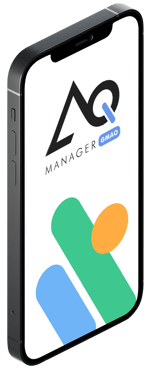
Vous devez être capable de centraliser les données ainsi que de fournir des rapports et des analyses clés. Il est dès lors essentiel d’être pourvu d’une solution mobile pouvant faciliter un dépannage efficace.
Une application mobile est un enjeu non négligeable de nos jours. Les techniciens sont constamment en mouvement, se déplaçant d'un actif à l'autre ou dépannant dans différentes usines ; ils doivent pouvoir accéder à des données complètes ainsi qu'à des observations et des travaux effectués sur les installations techniques ou sur les lieux d’intervention.
De plus, une application mobile vous permet de scanner le QR code ou le code barre d’un actif et ainsi d’accéder à son historique ou aux équipements identiques afin de vérifier si le problème n’a pas déjà été rencontré précédemment.
Ensuite, à l’aide du diagnostic de panne et à notre application, vous avez la possibilité d’explorer l’historique sur le terrain, de consulter quelles ont pu être les causes et, en conséquence, les remèdes appliqués précédemment pour régler ce problème. Cela permet de gagner du temps, soit en appliquant un remède qui a déjà été éprouvé lors d’une panne précédente ou bien d’éviter de perdre du temps à appliquer des remèdes inopérants.
Le diagnostic de panne est un excellent moyen de s'assurer que les budgets de maintenance sont concentrés sur les actifs les plus importants tout en minimisant les risques associés au fait de laisser certains actifs tomber en panne. Cependant, une stratégie de maintenance doit être documentée et évaluée en permanence car les coûts associés aux temps d'arrêt imprévus peuvent rapidement augmenter.
Une stratégie de maintenance efficace doit également inclure une maintenance préventive pour les actifs de grande valeur, et il n'y a pas de meilleur moyen de mettre en œuvre la bonne stratégie de maintenance qu'avec un outil de GMAO.
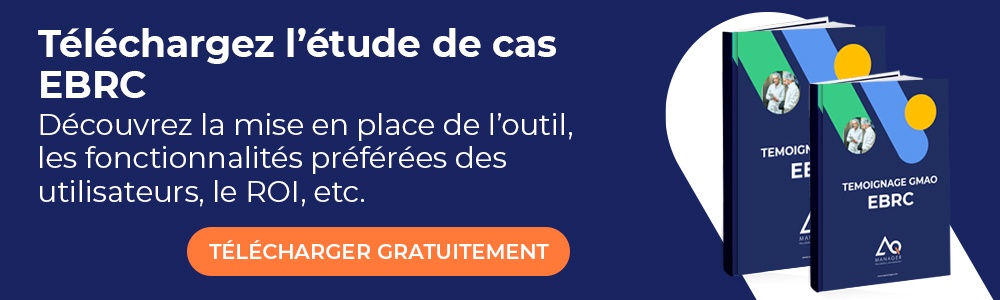