Dans le secteur industriel, les opérations de production dépendent fortement de la performance de vos équipements. C’est pourquoi il est majeur d'optimiser quotidiennement leurs performances.
En parallèle, votre service de production est confronté à une multitude de risques : des actifs vieillissants, des exigences environnementales, de sécurité et de conformité réglementaire de plus en plus strictes, des technologies émergentes et d'autres défis associés à la propriété et à l'exploitation des actifs.
Avant d’établir des actions préventives ou correctrices, il est de votre devoir de déterminer la criticité des équipements industriels, qui demeure un enjeu pour les analyses des risques industriels et la détermination des stratégies de maintenance.
La criticité des équipements industriels et son analyse, une approche en profondeur
Comment définir la criticité des équipements industriels ?
Commençons par le commencement. Qu’est-ce qu’un risque ? Un risque peut être défini comme un effet indésirable potentiel. Il en existe une multitude : des risques pour la sécurité, des risques matériels, des risques humains ou encore des risques portés sur la propriété intellectuelle.
Une usine possèdent parfois des centaines d’équipements fortement sujets à des risques tels que l’usure, l’érosion, la détérioration, le vieillissement, etc. Un défi quotidien qui nécessite une attention particulière car cela peut entrainer de véritables conséquences pour votre production.
L’un des outils qui a la capacité de vous aider dans l’évaluation des conséquences et de la probabilité de défaillance d'un élément spécifique au sein de votre système est l’évaluation de la criticité.
Ce terme aux allures barbares détermine ainsi quelles sont les caractéristiques qui rendent un équipement davantage critique par rapport aux autres. Chacun d'entre eux a un rôle unique avec un indice de criticité différent. Par exemple, les machines hautement critiques sont celles dont la production dépend le plus. Si aucune solution n’est mise en place pour pallier ce problème, elle peut tout bonnement s'arrêter ou des goulots d'étranglement peuvent se produire.
La criticité est donc la conséquence de la défaillance en termes de santé, de sécurité, d'environnement, de perte de production et de coût de maintenance.
Effectuer une analyse de la criticité pour une meilleure stratégie de maintenance
L’analyse de criticité vous permet de comprendre les risques potentiels de l’actif qui pourraient avoir un impact sur vos opérations.
Une analyse de criticité formelle vous aide à hiérarchiser efficacement le travail, à gérer les risques de manière appropriée et à baser les améliorations de la fiabilité sur des données objectives.
Par définition, il s’agit d’une analyse quantitative des défauts des équipements, et leur classement par ordre de conséquences graves sur la sécurité, l'environnement, les pertes de production et les coûts de maintenance.
Il est important de savoir à quel point chaque pièce d'équipement est essentielle pour la production et cela aidera à déterminer quelles actions préventives ciblées sont nécessaires pour réduire les temps d'arrêt lorsqu'ils se produisent, ainsi que pour les prévenir complètement.
Lorsqu'une machine s'arrête, elle peut rapidement dégénérer. Cette analyse amènera donc votre équipe à réfléchir à la cause de la panne et à évaluer quels sont ses besoins.
Téléchargez le replay de notre précédent webinaire et apprenez comment mesurer les performances de vos activités de maintenance :
Le score de criticité peut être utilisé comme entrée pour aider à déterminer le classement de priorité final pour les tâches de maintenance, qui à son tour peut être utilisé avec la priorité de l’ordre de travail.
Le but de cette analyse est donc de fournir les moyens pour reconnaître les équipements à haute criticité par rapport aux équipements à faible criticité, de réduire le niveau d'incertitude et de se concentrer sur les tâches de maintenance hautement prioritaires. L'analyse permet également de sélectionner la stratégie de maintenance la meilleure et la plus économique et de décider de l'assurance et de la demande de pièces de rechange.
Les équipements critiques peuvent être divisés en plusieurs groupes :
Les équipements primordiaux
Les actifs stratégiques correspondent aux équipements qui déterminent directement la capacité de l'entreprise à réussir, et dans quelle mesure. Ces équipements nécessitent une attention et un suivi permanents, qu'ils soient neufs ou non. La maintenance doit y être à son maximum.
Les équipements critiques
Les équipements critiques sont ceux qui doivent être en état de marche pour que votre entreprise puisse réaliser des bénéfices. Les performances sont moins importantes que le fait que l'équipement soit en service ou non. Si les équipements tournent, votre organisation a la capacité de produire du chiffre d'affaires. Le temps de fonctionnement est l'indicateur de performance clé.
Les équipements semi-critiques
Les équipements semi-critiques n'empêchent pas nécessairement la production lorsqu'ils tombent en panne. Ils mettent cependant le système à rude épreuve. Il est envisageable qu'une entreprise ou un processus puisse encaisser la perte d'un équipement semi-critique temporairement. La situation peut cependant vite dégénérer et le processus devenir trop instable.
Les équipements non critiques
Les équipements non critiques n'affectent pas la capacité de votre entreprise à générer des revenus, quels que soient leur taille, leur coût ou leur complexité.
Des avantages qui contribuent à une amélioration à 360°
Ce système fait partie des nombreuses mesures proactives et préventives qui vous aident à hiérarchiser vos ressources et à conduire des améliorations. Voici les principaux avantages que peut vous procurer une analyse de la criticité des équipements :
- L’identification des stratégies d’atténuation des risques de haut niveau pour des équipements spécifiques,
- La détermination du nombre optimal de pièces de rechange pour chaque équipement et donc, à optimiser les stocks,
- Une contribution dans les discussions sur le budget, de sorte que les équipements de haute criticité reçoivent une priorité plus élevée pour les mises à niveau ou le remplacement,
- La réduction des pannes critiques, des interventions de maintenance et des temps d'arrêt inutiles, et, en conséquence, l’amélioration de la sécurité,
- L’optimisation du programme de maintenance,
- L’optimisation des ressources.
Comment effectuer une analyse de criticité des équipements ?
Il n'y a pas de méthode unique pour effectuer l’analyse de criticité. Cela peut être très complexe car chaque installation et chaque composant individuel est différent.
Votre équipe de maintenance, par exemple, va se concentrer sur les équipements dont la maintenance est plus longue et plus difficile à réaliser ou dont les interventions de maintenance sont plus fréquentes.
Pour votre responsable de l'exploitation de l'usine, la réponse peut être différente : il s’agit de la machine qui génère un goulot d'étranglement ou celle qui a la plus grande capacité de production.
Mais alors, par où devriez-vous commencer ?
La méthode AMDEC (Analyse des Modes de Défaillance, de leurs Effets et de leur Criticité)
La méthode AMDEC, comme son nom l’indique, est une méthode utilisée pour identifier les modes de défaillance d’un produit, des moyens de production ou d’un processus. Il lui existe un homologue américain, la FMEA, qui est légèrement différente.
Elle se déroule en plusieurs étapes majeures :
1. Préparation de l’étude et constitution de l’équipe
Cette étape met les participants au cœur de l’action. Ces derniers doivent s’appuyer sur leur expérience. Chaque membre du groupe doit être sensibilisé un minimum au préalable à la méthode et met en commun ses compétences dans une démarche constructive.
2. Analyse fonctionnelle du procédé
En amont, il est nécessaire de connaitre et de comprendre le produit, le procédé ou le processus traité pour définir le périmètre de votre étude et pouvoir l’analyser. Vous devez répondre aux questions clés suivantes grâce à l’analyse fonctionnelle :
Quelle est la fonction d’usage ? Quelles sont les fonctionnalités attendues ? Quelles sont les contraintes ? Quelles sont les fonctions techniques ?
Lors de cette phase, les objectifs et les limites de l’étude sont définis.
3. Identifier les défaillances potentielles
Cette étape a pour but de lister toutes les défaillances potentielles qui peuvent survenir lors de la réalisation des tâches du procédé étudié. Il est également important d’identifier, pour chacune de ces défaillances, les effets et les causes, pour pouvoir mieux les limiter. Pour identifier les causes, il est possible d’utiliser l’arbre des causes, qui est un processus, une représentation graphique qui permet de comprendre pourquoi les pannes se sont produites.
> Diagnostic de pannes : premiers pas avec la GMAO
4. Evaluer les défaillances et déterminer la criticité
Lors de cette phase, vous avez la possibilité d’attribuer à chaque défaillance potentielle un indice de criticité. La criticité est la résultante de la combinaison de trois facteurs :
- La gravité de la défaillance et de l’effet (G) : conséquence plus ou moins grave pour l’utilisateur ;
- La fréquence d’apparition de la défaillance, l’occurrence (O) ;
- La probabilité de non-détection (D) : la défaillance se produit et il y a risque de ne pas la détecter.
Vous devez définir une échelle pour chaque facteur. Vous retrouverez couramment une échelle allant de 1 à 4 ou de 1 à 10. 1 étant une gravité/occurrence/probabilité faible, 10 étant une gravité/occurrence/probabilité forte.
5. Réduire les défaillances / suivre les actions
Après avoir classé les différents modes de défaillance, deux solutions s’offrent à vous : supprimer ou réduire la défaillance.
Dans le deuxième cas, vous pouvez rechercher des solutions par des actions correctives et / ou préventives dans le but d’obtenir une criticité plus faible. Pour chaque action, un responsable doit être désigné.
Finalement, il faut procéder à la planification des actions à mettre en œuvre et suivre leur efficacité et pertinence tout au long du projet.
Comment un logiciel de gestion de maintenance peut-il vous aider ?
Un système informatisé de gestion de la maintenance (GMAO) vous permet de suivre de manière hiérarchique chaque actif de votre organisation. Le suivi est nécessaire pour surveiller les calendriers de maintenance, les enregistrements de pannes et même les données de performances en temps réel.
La GMAO vous accompagne notamment dans la collecte de données, le classement des actifs, ainsi que la mise en œuvre et le suivi de la stratégie.
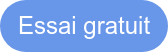
Dans un premier temps, une solution logicielle représente un véritable registre de données pour l’analyse avec la possibilité de répertorier les équipements, d’avoir une vue sur leur fiche technique et d’enregistrer les différentes pannes. L'équipe en charge de ce processus de criticité peut alors fonder ses évaluations sur des données et des informations empiriques, qui peuvent également être partagées et utilisées par tous.
Une fois que la criticité est calculée, une stratégie peut être identifiée. La GMAO gère la planification des tâches, les ressources et les pièces de rechange nécessaires pour mettre en œuvre l'atténuation des risques.
Ensuite, l'objectif principal de l'analyse de criticité est d'atténuer les risques, ce qui constitue un avantage important pour votre entreprise. En déterminant où les pannes sont susceptibles de se produire et en donnant la priorité à celles qui seraient les plus préjudiciables, vous êtes mieux en mesure de planifier des tâches de maintenance et de révision efficaces.
Finalement, avec moins de temps consacré à la planification et à l'exécution de tâches inutiles grâce à la GMAO, et avec une incidence moindre d'événements d'indisponibilité coûteux, les coûts de fonctionnement de vos installations deviennent plus rationalisés. Les entreprises qui effectuent une analyse de criticité efficace peuvent voir des dépenses réduites (ou tout du moins, des ressources utilisées plus efficacement) dans les domaines suivants :
- Planification et ordonnancement de la maintenance préventive
- Temps d'arrêt des équipements
- Gros travaux de réparation
- Accidents et responsabilité civile
- Coûts de remplacement des actifs
Maintenir le fonctionnement d’actifs coûteux tout au long de leur cycle de vie nécessite une stratégie bien établie. À mesure que les volumes augmentent, que la demande s’accélère ou que les produits se diversifient, les pannes d'actifs, même les plus petites ou temporaires, érodent votre fiabilité opérationnelle.
La gestion des équipements critiques nécessite donc un processus et une analyse de criticité des équipements bien ancrés pour garantir la réduction des risques opérationnels.
La GMAO peut être un outil puissant dans le suivi et l'organisation des données nécessaires à l'élaboration de politiques des risques et pour faire face à la baisse des performances des actifs ou à une panne imminente bien avant qu'elle ne vienne entraver la productivité.
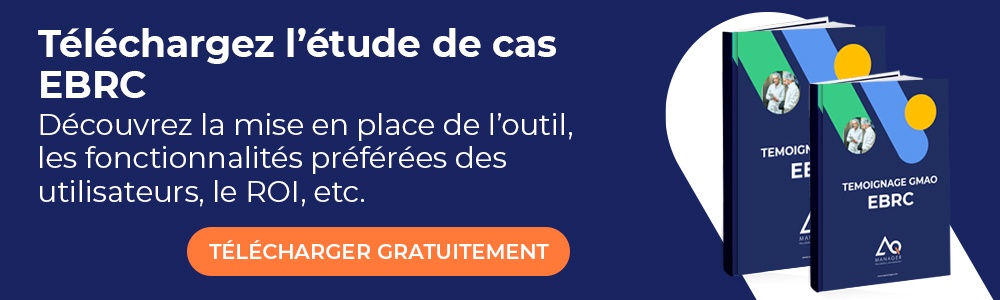