Vous trouvez que le coût de votre maintenance est en train de grignoter une part de plus en plus importante de votre budget ?
Avec l'augmentation des coûts divers et de l’inflation, il est plus que jamais important de capitaliser sur une stratégie proactive pour maximiser la disponibilité et la fiabilité des équipements tout en minimisant les coûts de maintenance.
Alors que les méthodes de maintenance basique peuvent ne plus suffire, la maintenance conditionnelle vous permet de surveiller en continu l'état des équipements de production grâce à la technologie et à l'analyse de données.
Dans cet article, nous vous expliquons en détail ce qu'est la maintenance conditionnelle et comment l’intégrer à votre stratégie en plusieurs étapes.
La maintenance conditionnelle : une stratégie proactive pour la disponibilité de vos équipements
Vos machines de production doivent fonctionner en continu pour répondre à la demande des clients. Mais que se passe-t-il si une machine tombe en panne ? La production est interrompue, les délais sont retardés, et les coûts de réparation s'accumulent. C'est là que la maintenance conditionnelle entre en jeu.
La maintenance conditionnelle repose sur la surveillance constante de l'état de vos installations de production pour détecter toute anomalie ou défaillance avant qu'elle ne se produise. Pour ce faire, des capteurs et des instruments de mesure sont installés sur les machines afin de collecter des données en temps réel sur leur fonctionnement, et bien plus encore. Ces données sont ensuite analysées à l'aide d'algorithmes et d’un logiciel de maintenance (GMAO) pour détecter les signes précurseurs d'une panne.
Ainsi, les réparations peuvent être planifiées avant que la panne ne se produise, ce qui évite les interruptions de production et réduit les coûts de maintenance.
Distinguer maintenance conditionnelle et maintenance 4.0
Même si la maintenance conditionnelle et la maintenance 4.0 ont des points communs, elles utilisent des méthodes et des technologies différentes. La première se base sur la surveillance régulière des équipements grâce à des paramètres bien spécifiques, tels que la température, les vibrations ou la pression. Vos interventions sont ainsi mieux gérées en fonction des conditions réelles de vos installations.
La maintenance 4.0, quant à elle, utilise des technologies plus avancées, comme l'intelligence artificielle ou l’apprentissage automatique, pour optimiser la maintenance. Elle utilise des capteurs connectés pour collecter des données en temps réel, qui sont ensuite analysées à l'aide d'algorithmes pour prévoir les pannes et les défaillances.
Finalement, les deux approches ont le même but : maximiser la disponibilité et la fiabilité des équipements tout en minimisant les coûts de maintenance.
➡️ Transformez votre stratégie avec la maintenance conditionnelle : inscrivez-vous à notre webinaire gratuit du 15 octobre pour apprendre à prioriser vos équipements efficacement.

Etape 1 : évaluer les besoins de votre entreprise en termes de maintenance conditionnelle
La maintenance conditionnelle, c'est bien, mais avant de vous lancer, il est nécessaire d’évaluer les besoins spécifiques de votre entreprise. Pourquoi ? Car chaque organisation est unique et possède des processus différents qui nécessitent des approches de maintenance adaptées.
Dans un premier temps, vous devez identifier vos équipements les plus critiques, afin de choisir les techniques de maintenance conditionnelle les plus adéquates. Pas de panique, on vous guide !
Comment identifier vos équipements les plus critiques ?
Afin de minimiser les perturbations dans la production et de maximiser la rentabilité, une approche méthodique est nécessaire. Une fois les actifs de votre structure identifiés, l’évaluation des risques est la clé.
Analyse de l’impact potentiel général
Tout d'abord, il est important de déterminer l'impact potentiel des pannes de chaque machine sur la production, la sécurité des travailleurs, la qualité des produits, et la réputation de l'entreprise. Par exemple, une panne d'une machine de production clé, telle qu’une machine d’assemblage de moteurs, peut entraîner une perte importante de production, mettre en danger la sécurité des travailleurs, et altérer la qualité des produits. Ces équipements doivent ainsi être considérés comme critiques.
Analyse des données de maintenance
L’analyse des données de maintenance peut aider à identifier les machines qui ont le plus souvent des pannes ou des défaillances. Par exemple, une machine qui nécessite une maintenance fréquente ou coûteuse peut être considérée comme critique pour l'entreprise.
Analyse de la valeur financière et durée de vie
Les équipements qui ont une grande valeur financière ou une longue durée de vie peuvent également être classés comme critiques. Par exemple, les machines-outils, les équipements de production automatisée, les transformateurs électriques, et les générateurs de secours sont souvent des machines coûteuses dont la panne peut entraîner des perturbations significatives dans la production et des coûts élevés de réparation.
Analyse de la criticité
En tenant compte de tous ces facteurs, vous avez désormais la possibilité d’établir la criticité de chaque équipement et de les classer en fonction de leur importance.
Etape 2 : choisir les paramètres de maintenance conditionnelles adaptées à vos équipements
Il est ensuite crucial de sélectionner les techniques de maintenance conditionnelle appropriées. Mais comment faire le bon choix ?
Analyse des vibrations
Parmi les techniques les plus populaires, l'analyse vibratoire vous permet de déceler les anomalies de vos équipements à partir de la mesure de leurs vibrations. C'est la méthode idéale pour détecter les soucis sur des moteurs, des pompes ou des compresseurs. Mais attention, il vous faudra investir dans du matériel de mesure et des compétences techniques pour bien interpréter les résultats.
Analyse d’huile
Une autre technique, plutôt commune, repose sur l'analyse d'huile, qui permet de détecter les anomalies dans les équipements à partir de l'analyse de l'huile lubrifiante. Cette technique est particulièrement adaptée aux engrenages, aux boîtes de vitesses, et aux turbines. Elle est relativement simple à mettre en œuvre et peut être réalisée par du personnel ayant des compétences de base en maintenance.
Analyse thermographique
Particulièrement adaptée aux équipements électriques (panneaux de distribution, transformateurs, les moteurs électriques et connexions électriques), cette technique consiste à mesurer la température à l'aide d'une caméra thermique pour détecter les zones de surchauffe qui pourraient indiquer des problèmes tels que des défauts d'isolation, des pertes de charge électrique, ou des frottements excessifs.
Analyse des signaux électriques
Cette méthode implique la surveillance des signaux électriques des équipements, tels que les moteurs électriques, transformateurs, générateurs, etc., pour détecter les anomalies qui pourraient indiquer des problèmes tels que des pertes de charge, des déséquilibres, des surtensions ou des sous-tensions.
Inspection visuelle
Veille comme le monde, cette technique consiste à inspecter visuellement les équipements (tuyaux, réservoirs, châssis, etc.) pour détecter les anomalies telles que des fissures, des fuites, et des signes d'usure.
Techniques de contrôle non destructif
Enfin, les techniques de contrôle non destructif telles que les ultrasons, les courants de Foucault, la magnétoscopie et les rayons X peuvent également être utilisées pour détecter les déviances dans les équipements. Cependant, ces techniques nécessitent des compétences spécialisées pour leur mise en œuvre et peuvent être plus coûteuses.
➡️ Transformez votre stratégie avec la maintenance conditionnelle : inscrivez-vous à notre webinaire gratuit du 15 octobre pour apprendre à prioriser vos équipements efficacement.

Etape 3 : utiliser vos données de manière proactive
Les données collectées lors des activités de maintenance conditionnelle sont de véritables mines d'or pour tout un chacun dans votre service de maintenance. De la collecte à l’exploitation de ces dernières, elles permettent d'avoir une vision globale de l'état des équipements et des interventions réalisées, ce qui facilite la planification des opérations de maintenance.
Vos opérateurs peuvent également identifier les tendances et les causes profondes des problèmes. Par exemple, si une machine tombe en panne régulièrement, l'analyse des données peut permettre de détecter un problème sous-jacent, tel qu'une usure prématurée des pièces ou une mauvaise utilisation de la machine.
L'avantage de cette approche est qu'elle permet également d'améliorer les pratiques de maintenance, comme un artisan perfectionne ses techniques pour devenir le meilleur dans son domaine, et de prendre des décisions éclairées sur la modification, la réparation ou le remplacement des machines.
La GMAO, une approche centralisée et organisée pour vos données
Et pour gérer toutes ces données, la GMAO s’avère être l’outil le plus adéquat. Dans ce type de logiciel, les données sont gérées de manière centralisée et organisée afin d'optimiser la maintenance des équipements. Les informations collectées sur les machines, telles que leur état, leur historique de maintenance et leurs caractéristiques, sont stockées dans une base de données. Cette base de données est accessible à tous les membres de l'équipe, leur permettant ainsi de suivre les informations en temps réel.
Etape 4 : planifier et organiser vos opérations et interventions
Pour s'assurer que les équipements sont entretenus de manière régulière et préventive, il est crucial d'établir un calendrier. Mais comment créer un calendrier qui fonctionne pour votre entreprise ? Il est important de prendre en compte la fréquence de la maintenance, la durée de vie des équipements et le niveau de risque associé à chacun d’entre eux.
En travaillant en collaboration avec les responsables de la production, vous pouvez élaborer un calendrier flexible qui s'adapte aux besoins changeants de l'entreprise. Ainsi, vous pouvez vous assurer que vos machines restent en bonne santé sur le long terme.
Plusieurs types de plannings sont disponibles dans une application de GMAO, pouvant être interfacée avec d’autres systèmes au sein de votre service. Les plannings étant tous synchronisés entre eux, la planification des interventions y est rendue dynamique par un système de glisser-déposer. La modification d’un horaire de travail ou le déplacement d’une intervention y sont donc facilement réalisables. La planification s’adapte également en fonction du plan de production.
Etape 5 : former votre personnel à la réalisation de la maintenance conditionnelle
La formation du personnel à l'utilisation des techniques de maintenance conditionnelle est également un aspect clé pour garantir l'efficacité de la maintenance. Le personnel doit être formé aux différentes méthodes, aux outils de mesure et d'analyse, et aux procédures.
Et comme pour toute formation, elle doit être continue pour garantir que votre personnel dispose des compétences et des connaissances les plus récentes en matière de maintenance conditionnelle. Avec une équipe bien formée, vous pouvez améliorer l'efficacité de votre service et prolonger la durée de vie de vos équipements.
👨💻 Optimisez la durée de vie de vos équipements avec la maintenance conditionnelle : inscrivez-vous à notre webinaire gratuit le 15 octobre et apprenez à anticiper vos priorités.

Etape 6 : évaluer l’efficacité du programme mis en place
L'évaluation régulière de l'efficacité du programme est essentielle pour garantir que les équipements sont maintenus de manière efficace et rentable. Pour ce faire, il est important de mesurer son impact sur la fiabilité, les temps d'arrêt, les coûts de maintenance, et d'autres facteurs pertinents pour l'entreprise.
Utiliser des indicateurs adaptés à la stratégie de votre maintenance
Vous l’avez compris, pour obtenir de bons résultats et prendre de meilleures décisions, il est nécessaire d’améliorer le rendement et les performances de vos installations.
Grâce à un tableau de bord dynamique et en filtrant les données sur une période de temps sélectionnée et précise ainsi que sur les différentes ressources, un tableau de bord efficace vous permet de :
- Visualiser l’état et la disponibilité de chaque équipement
- Prioriser différemment, en fonction de vos choix stratégiques ;
- S'assurer que l’ensemble des contrôles réglementaires est respecté ;
- Visualiser les disponibilités des équipements à tout moment et de n’importe quel endroit ;
- Visualiser la répartition des ordres de travaux ; ou encore
- Surveiller les tendances (pannes fréquentes ou signes avant-coureurs de défaillance).
Adapter le programme aux besoins de l’entreprise
Enfin, l'ajustement du programme de maintenance conditionnelle en fonction des besoins de l'entreprise est essentiel pour garantir l'efficacité continue de celui-ci. Vos responsables de maintenance doivent être en mesure de l’ajuster en fonction des nouvelles tendances et des changements dans les besoins de l'entreprise.
La maintenance coûte cher, c'est un fait. Mais avec la maintenance conditionnelle, vous pouvez éviter les pannes imprévues et maximiser la disponibilité de vos équipements, tout en réduisant les coûts. Grâce aux techniques de surveillance, à la GMAO et à une équipe bien formée, vous pouvez devenir le héros de la maintenance dans votre entreprise !
Alors n'attendez plus, planifiez votre stratégie de maintenance conditionnelle dès aujourd'hui.
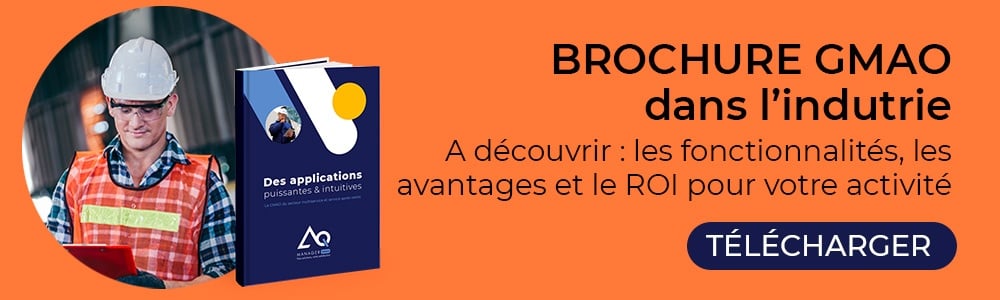