Trouver l'équilibre parfait entre préventif et correctif : est-ce la clé de la maintenance industrielle en 2024 ?
Dans l'univers complexe et en constante évolution de l'industrie, la maintenance transcende son rôle traditionnel pour devenir un facteur crucial de performance et de durabilité. Les entreprises, investissant massivement dans des équipements de pointe, sont désormais confrontées à un défi majeur : comment gérer ces machines avancées pour maximiser leur rendement et leur longévité ?
Entre l'art de la prévention et la science de la réaction, découvrez comment un équilibre stratégique en maintenance peut transformer le paysage industriel et mener à une productivité sans précédent.
Maintenance préventive et corrective : rappels
La maintenance corrective, c'est l'art de répondre à l'appel imprévu de la machine en détresse. Comme un médecin urgentiste face à son patient, le technicien de maintenance s'engage dans une course contre la montre pour réparer l'équipement défaillant. Cette approche est réactive par nature : elle attend que le problème surgisse pour agir. Si l'on peut comparer les équipements industriels à un orchestre, la maintenance corrective intervient lorsque l'une des instruments cesse soudainement de jouer sa mélodie, perturbant l'harmonie de l'ensemble.
Imaginez un technicien confronté à une chaîne de production soudainement interrompue ; son rôle est de diagnostiquer rapidement le problème, de remplacer une pièce défectueuse ou de réparer un composant endommagé.
La maintenance préventive, quant à elle, est perçue non seulement comme une routine d'entretien, mais comme une stratégie globale d'optimisation des ressources et de préservation de l'intégrité des équipements. Elle s'articule autour d'une compréhension approfondie du fonctionnement et de la durée de vie des composants et équipements. Les professionnels, armés de données historiques et de l'analyse prédictive, peuvent ainsi identifier les signes avant-coureurs de défaillances potentielles. Par exemple, un technicien expérimenté saura reconnaître l'usure anormale d'un roulement à bille bien avant qu'il ne cause un arrêt complet de la machine.
La maintenance corrective : un double tranchant en milieu industriel
Lorsqu'une machine tombe en panne, la maintenance corrective entre donc en jeu. Bien qu'elle semble réactive et moins idéale, cette approche a ses mérites dans certains contextes. Pour les équipements moins critiques ou dont les défaillances sont imprévisibles et peu coûteuses, la maintenance corrective peut être économiquement viable. Cependant, les coûts cachés, tels que l'arrêt imprévu de la production, l'usure accélérée d'autres équipements, et le stress sur le personnel, doivent être considérés. Le défi réside ainsi dans l'évaluation précise de ces coûts indirects.
La maintenance préventive : une stratégie nuancée pour les professionnels
Dans le milieu industriel, la maintenance préventive est perçue non seulement comme une routine d'entretien, mais comme une stratégie globale d'optimisation des ressources et de préservation de l'intégrité des équipements. Elle s'articule autour d'une compréhension approfondie du fonctionnement et de la durée de vie des composants. Les techniciens et responsables de maintenance, armés de données historiques et de l'analyse prédictive, peuvent ainsi identifier les signes avant-coureurs de défaillances potentielles.
Elle est souvent perçue comme une stratégie plus proactive et moins coûteuse à long terme. Cependant, sa mise en œuvre excessive conduit à ses propres problèmes. Remplacer des pièces qui pourraient encore fonctionner pendant une période significative entraîne des coûts matériels et des interruptions de travail. De plus, la maintenance préventive excessive peut induire une complaisance, où les opérateurs deviennent moins vigilants à la détection des signes avant-coureurs de défaillance.
Quand se retrouve-t-on à devoir choisir entre les deux ?
Le choix entre maintenance préventive et corrective, et la recherche d'un équilibre optimal entre les deux, est crucial et intervient dans divers contextes. Que ce soit lors de la planification des opérations de maintenance, face à des contraintes budgétaires, en raison de limitations de temps et de ressources, ou lors de l'évaluation de la criticité des équipements, cette décision impacte directement l'efficacité et la durabilité de la production. L'objectif est de maximiser la performance et la disponibilité des équipements tout en minimisant les coûts opérationnels et les interruptions, un défi qui nécessite une analyse continue et adaptative.
L'art de l'équilibre : combiner les deux approches
L'équilibre entre les stratégies préventives et correctives est un art subtil, exigeant une compréhension profonde des mécanismes techniques et une analyse fine des données opérationnelles. Cette harmonisation est cruciale pour une gestion efficace des équipements, impactant directement la productivité et la durabilité des installations.
En effet, une application excessive de la maintenance préventive peut mener à des inefficacités. Des inspections et des remplacements trop fréquents de pièces qui sont encore fonctionnelles peuvent entraîner une augmentation des coûts opérationnels. De plus, cela peut conduire à un faux sentiment de sécurité, où les problèmes non détectés lors des inspections régulières peuvent s'aggraver en pannes majeures.
D'un autre côté, la maintenance corrective intervient là où la maintenance préventive ne suffit pas, traitant les problèmes inattendus qui surviennent malgré les meilleures pratiques préventives. La capacité à répondre efficacement aux pannes imprévues reste donc un élément clé de la stratégie de maintenance globale.
La quête du juste milieu : une dynamique constante
L'interdépendance entre maintenance préventive et corrective est une danse délicate où chaque mouvement doit être soigneusement calculé. Le juste milieu n'est pas un point fixe, mais plutôt un objectif fluctuant qui varie en fonction de nombreux facteurs, tels que l'usure des équipements, les conditions d'exploitation, et les retours d'expérience. Par exemple, une presse hydraulique dans une usine de fabrication peut nécessiter des inspections préventives trimestrielles, tandis qu'une fraiseuse CNC dans le même environnement pourrait exiger un contrôle mensuel en raison de son utilisation intensive.
L'Analyse des données : un pilier de la stratégie
Dans cet équilibre, l'analyse des données joue un rôle primordial. Ces chiffres et statistiques, loin d'être de simples nombres, sont les boussoles qui guident nos décisions. Ils nous aident à dessiner une stratégie qui s'adapte non seulement aux besoins actuels des équipements mais aussi aux stratégies futures.
L'exploitation des historiques de maintenance, des enregistrements de pannes et des données de performance des équipements permet de développer une compréhension approfondie des cycles de vie des machines et de leurs composants. Ces données, lorsqu'elles sont correctement analysées, peuvent révéler des tendances et des modèles prédictifs. Par exemple, une augmentation progressive du bruit ou des vibrations dans un moteur peut indiquer une usure imminente, permettant de planifier une intervention préventive avant une panne complète.
Par exemple, si une usine de production enregistre une augmentation de 15% des pannes sur une ligne d'assemblage au cours des six derniers mois, l'analyse des données peut révéler que la majorité des défaillances provenaient d'un composant spécifique. En ajustant la fréquence de maintenance préventive de ce composant, les pannes ont été réduites de 10%, améliorant la productivité globale.
L'Importance de la flexibilité et de l'adaptabilité ou quand prévention rime avec précision
Une stratégie de maintenance efficace requiert une flexibilité et une adaptabilité constantes. La maintenance préventive n'est pas une recette à appliquer aveuglément. C'est un art délicat qui demande de savoir quand et comment agir. Changer une pièce trop tôt ou trop tard peut coûter cher. L'astuce ? Une surveillance attentive et une réaction mesurée.
Les techniciens et les gestionnaires doivent également être prêts à ajuster leurs plans de maintenance en fonction des retours d'expérience et des changements dans les conditions opérationnelles. Par exemple, une augmentation des demandes de production peut nécessiter des ajustements dans la fréquence de la maintenance préventive pour éviter des arrêts inopportuns.
Autre exemple : Dans une centrale électrique, le remplacement préventif des turbines est planifié tous les 5 ans. Cependant, une analyse approfondie a montré que ces turbines pouvaient fonctionner efficacement pendant 7 ans sans risque majeur. En ajustant le cycle de remplacement, la centrale a économisé environ 20% des coûts de maintenance sur cette opération.
Êtes-vous prêt à révolutionner votre stratégie de maintenance ? Demandez une démo gratuite de notre logiciel de GMAO :

Technologies et outils pour un équilibre optimal en maintenance
L'adoption de technologies avancées joue un rôle crucial dans l'atteinte d'un équilibre efficace entre maintenance préventive et corrective. Des outils comme un logiciel de gestion de maintenance (GMAO) ou l'Internet des Objets (IoT) et les systèmes d'analyse de données transforment la manière dont la maintenance est planifiée et exécutée.
Logiciel de gestion de maintenance (GMAO)
Un système de GMAO est un outil informatique conçu pour faciliter la gestion intégrale des activités de maintenance, ainsi que la supervision des ressources et matériels dédiés à l'entretien au sein de votre entreprise.
Avant l'avènement de ces technologies, les sociétés devaient effectuer un suivi manuel des tâches de maintenance et mettre à jour ces informations de manière conventionnelle. Aujourd'hui, grâce à ce logiciel de gestion, il est possible de stocker toutes les données relatives aux opérations de maintenance de manière détaillée et de monitorer efficacement l'état des équipements essentiels.
Les solutions de GMAO actuelles sont hautement spécialisées, répondant de façon toujours plus précise aux exigences spécifiques du domaine de la maintenance. Elles s'appuient sur une vaste gamme de savoir-faire et de compétences techniques, adaptées aux différents secteurs d'activité. Ces systèmes offrent une fonctionnalité étendue, permettant l'automatisation de processus tels que :
L’un des plus gros avantages de ce type de solution réside dans sa compréhension des métiers de la maintenance. La GMAO évolue rapidement pour s’adapter aux nouvelles pratiques (maintenance 4.0 ou maintenance conditionnelle) et aux nouvelles technologies.
Cela peut inclure des fonctionnalités telles que :
- La connectivité en temps réel des équipements et des données de maintenance pour une meilleure visibilité et une analyse en temps réel de la performance des équipements,
- L'intégration de l'Internet des objets (IoT) pour permettre la surveillance à distance des équipements et la détection des anomalies,
- L'utilisation d'algorithmes d'apprentissage automatique pour prédire les besoins de maintenance et optimiser les plans de maintenance.
En somme, les progiciels de gestion de maintenance évoluent pour offrir une meilleure automatisation, une meilleure prévisibilité et une meilleure communication dans le but d'améliorer l'efficacité et la rentabilité.
Prêt à transformer votre approche de la maintenance industrielle ?
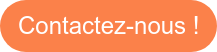
Cas de déséquilibre et coûts supplémentaires
Cependant, une utilisation inadéquate de ces technologies peut mener à des déséquilibres. Un exemple concret serait une entreprise s'appuyant excessivement sur des prédictions automatisées sans prendre en compte l'expertise humaine, menant à des remplacements inutiles de pièces et augmentant ainsi les coûts de maintenance. À l'inverse, une négligence dans l'utilisation de ces outils peut entraîner un manque de maintenance préventive, résultant en des pannes fréquentes et coûteuses.
Conseils Pratiques pour 2024 : conjuguer expertise et technologique
Pour réussir en 2024, il est essentiel de conjuguer expertise humaine et technologie, en respectant ces quelques principes clés. Et parfois, les conseils les plus simples sont les plus judicieux.
Prioriser la formation et l'expertise technique et intégrer les retours d’expérience
La compétence du personnel est au cœur de toute stratégie réussie. Investissez dans la formation continue pour que vos équipes soient au fait des dernières technologies et pratiques. Un technicien bien formé est capable de détecter les problèmes naissants, souvent invisibles à l'œil non averti.
Chaque incident de maintenance est une opportunité d'apprentissage. Documentez et analysez ces incidents pour affiner vos stratégies préventives. Par exemple, si un type spécifique de pompe tombe en panne régulièrement, examinez les causes profondes et ajustez votre plan de maintenance en conséquence.
Adopter une approche holistique
Considérez la maintenance non pas comme une série d'actions isolées, mais comme une partie intégrante de l'opération globale de l'entreprise. Cela signifie travailler en étroite collaboration avec les autres départements, comme la production et la logistique, pour garantir que la maintenance soutient les objectifs généraux de l'entreprise.
Optimisation des stocks de pièces de rechange
Utilisez la GMAO pour maintenir un inventaire optimal de pièces de rechange. Analysez les historiques de pannes pour anticiper les besoins en pièces, en évitant à la fois les surstocks coûteux et les ruptures de stock qui peuvent entraîner des temps d'arrêt prolongés.
Standardisation des procédures de maintenance
Élaborez des procédures de maintenance standard pour chaque type d'équipement. Cela garantit que toutes les interventions, qu'elles soient préventives ou correctives, sont effectuées de manière cohérente et complète.
L'Humain au cœur de la machine
Enfin, n'oublions jamais que derrière chaque machine, il y a des hommes et des femmes. Leur expertise, leur intuition, et leur capacité d'adaptation sont essentielles. Ils sont les véritables architectes de cette stratégie d'équilibre entre maintenance préventive et corrective.
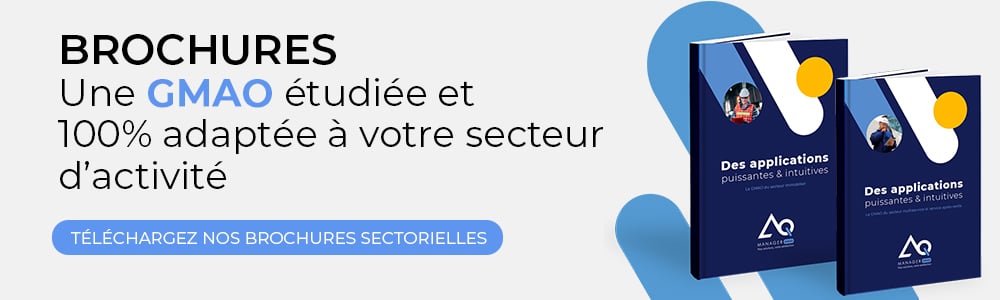