Et si vos opérateurs devenaient les gardiens de vos équipements ? Bien plus qu’une simple méthodologie, la maintenance autonome, ou maintenance premier niveau, est une philosophie qui responsabilise les équipes tout en renforçant la fiabilité de vos machines.
Née d’une culture d’amélioration continue, elle offre des solutions pragmatiques pour optimiser la production et réduire les pannes.
Découvrez comment cette approche peut transformer votre gestion de maintenance et la dynamique de vos équipes.
Qu’est-ce que la maintenance autonome et pourquoi est-elle stratégique ?
Si vous cherchez à adopter une stratégie de maintenance performante et durable, vous avez probablement déjà croisé ces concepts clés, tels les 5S (Seiri, Seiton, Seiso, Seiketsu, Shitsuke), la méthode Kaizen ou encore la maintenance productive totale (Total Productive Maintenance - TPM).
Pour rappel, la maintenance productive totale est une méthode de gestion de la maintenance visant à maximiser la performance des équipements en éliminant les pannes et les pertes, grâce à l'implication de tous les employés et à une amélioration continue.
Elle repose sur 8 piliers principaux et la mise en œuvre d’une telle méthode nécessite une approche structurée et une bonne coordination au sein de l'équipe, car chaque membre doit comprendre son rôle et l'importance de sa contribution.
La maintenance autonome est l’un des piliers de cette dernière et constitue une approche incontournable pour toute entreprise dont les objectifs sont d'améliorer l'efficacité opérationnelle, de réduire les temps d'arrêt, et de responsabiliser les équipes en leur donnant les outils nécessaires pour détecter et prévenir les dysfonctionnements.
En effet, les techniciens étant les plus proches des machines, ils jouent un rôle clé dans leur bon fonctionnement, notamment en appliquant les principes du Lean pour identifier les sources de gaspillage et optimiser les processus.
Les origines de la maintenance autonome
Introduite dans les années 1970 au Japon, la maintenance autonome est née dans le cadre de la TPM (Total Productive Maintenance).
Son objectif ? Transférer aux opérateurs principaux la responsabilité des tâches d’entretien de leurs équipements. Cette méthodologie repose sur les principes du Lean Manufacturing, une approche visant à éliminer les gaspillages sous toutes leurs formes : temps perdu, surconsommation de ressources, pannes imprévues, ou encore inefficacité des processus.
En leur confiant une part active dans l'entretien quotidien et la surveillance de leurs équipements, la maintenance autonome représente un véritable changement de culture qui responsabilise les équipes, améliore la fiabilité des machines et réduit les coûts liés aux interruptions non planifiées.
Finalement, en les responsabilisant, cela réduit la dépendance totale aux équipes de maintenance plus spécialisées et permet une intervention plus rapide.
Un retour à l’essentiel : l’humain avant tout
Cette stratégie s’est imposée comme un concept à part entière grâce à son impact direct sur le fonctionnement des entreprises.
Contrairement à d’autres aspects de la TPM qui s’intègrent dans une stratégie globale (la maintenance planifiée, par exemple, repose sur une analyse systématique des données, des prévisions budgétaires et des priorités opérationnelles. Elle exige une vision à long terme, des objectifs transversaux et une coordination des ressources), la maintenance autonome, quant à elle, repose sur une transformation profonde des pratiques quotidiennes.
Ce focus sur l’humain et la proximité avec les équipements lui donne une identité forte et universelle, parfois même en dehors du cadre de la TPM. C’est une méthode qui peut être adoptée indépendamment pour ses bénéfices immédiats : réduction des pannes, meilleure communication et montée en compétences des équipes.
Ainsi, la maintenance autonome transcende la TPM en devenant une pratique adaptable et accessible, alignée avec les besoins d’une production moderne.
Les bénéfices immédiats (et mesurables) de la maintenance autonome
La mise en place de la maintenance de premier niveau transforme donc rapidement la gestion des équipements et l’implication des équipes sur le terrain. Voici comment ses bénéfices se traduisent dans la réalité, avec des résultats visibles dès les premiers mois :
- Réduction des pannes imprévues : Ce système place les équipes au cœur de la prévention des pannes. Grâce à leurs inspections régulières des équipements, ils repèrent rapidement des signes avant-coureurs tels que des fuites, des usures ou des vibrations anormales.
Ces anomalies mineures, souvent invisibles pour les techniciens qui interviennent de manière ponctuelle, sont signalées ou corrigées directement par les opérateurs avant qu'elles ne deviennent des pannes coûteuses.
Ce travail de proximité complète les interventions plus techniques des techniciens, qui peuvent se concentrer sur les réparations complexes.
Résultat : moins de surprises, une meilleure disponibilité des équipements et une planification plus sereine.
- Augmentation de la disponibilité des équipements : En réduisant les arrêts imprévus, les machines restent opérationnelles plus longtemps. Cela signifie moins de temps perdu à attendre des réparations ou des pièces de rechange, et plus de temps consacré à produire. Cette disponibilité accrue a un impact direct sur la cadence de production et les délais respectés.
- Diminution des coûts de maintenance : En prenant en charge des tâches simples comme le nettoyage, la lubrification ou le resserrage de vis, les opérateurs limitent le recours à des interventions techniques coûteuses. Les réparations complexes et les interruptions prolongées deviennent moins fréquentes, ce qui se reflète directement dans les budgets de maintenance.
- Engagement accru des équipes : Donner aux opérateurs la responsabilité de leurs machines change complètement leur relation avec leur poste de travail.
Ils ne sont plus de simples exécutants, mais des acteurs impliqués dans la performance globale. Ce sentiment d’appartenance booste leur motivation et favorise une dynamique d’équipe plus positive.
- Gain en visibilité sur l’état des machines : Grâce à des inspections quotidiennes et systématiques, les opérateurs disposent d’une connaissance approfondie de leurs machines. Ce suivi régulier permet d’anticiper les problèmes avant qu’ils ne deviennent critiques, mais aussi de planifier des interventions au bon moment, en minimisant les interruptions.
Les étapes clés pour mettre en œuvre une stratégie de maintenance autonome réussie
Mettre en place l'auto-maintenance ne s’improvise pas. Pour garantir son succès, il est essentiel de suivre un plan structuré et de s’assurer que les équipes sont pleinement engagées dans cette démarche.
Voici les étapes incontournables :
1. Écouter les opérateurs et intégrer leurs retours
Avant même de structurer la démarche, commencez par dialoguer avec les opérateurs. Ce sont eux qui connaissent le mieux les équipements et leurs spécificités au quotidien. Leurs retours vous permettront d’identifier les zones à risques, les dysfonctionnements récurrents, et les besoins réels sur le terrain.
En les écoutant, vous instaurez aussi un climat de confiance, clé pour obtenir leur adhésion. Leur implication dès le départ renforce davantage leur sentiment de responsabilité et garantit que les routines mises en place sont réellement adaptées à la réalité du terrain.
2. Diagnostic initial des besoins
Avant de commencer, prenez le temps de poser un diagnostic précis. Analysez également les compétences actuelles : les équipes sont-elles déjà familières avec les machines ou ont-elles besoin d’un accompagnement plus poussé ?
Identifiez également les équipements qui bénéficieront le plus de cette approche. Par exemple, certains équipements critiques ou à forte fréquence d’utilisation peuvent être prioritaires.
Un diagnostic bien mené vous donnera une vision claire des actions à engager.
3. Formation et accompagnement
Une formation ciblée est indispensable. Construisez un programme progressif et adapté, qui commence par les bases (nettoyage, inspection) avant d’introduire des interventions plus techniques.
N’oubliez pas l’accompagnement sur le terrain : un opérateur formé mais non soutenu risque de perdre ses réflexes. Pensez aussi à désigner des référents pour guider et encourager les équipes.
4. Standardisation des pratiques
La clé de l'auto-maintenance, c’est la régularité.
Et pour y parvenir, mettez en œuvre des outils simples mais efficaces :
- Check-lists d’inspection,
- Routines quotidiennes,
- Guides visuels pour le nettoyage,
- Lubrification,
- Etc.
Ces standards garantissent que vos employés travaillent de la même manière, ce qui facilite le suivi et limite les oublis.
Personnalisez ces routines selon les équipements pour maximiser leur efficacité.
5. Mise en place des outils adaptés
Facilitez le travail de vos équipes en leur fournissant les outils nécessaires : pensez à intégrer un système de remontée d’informations automatique via une application telle que la GMAO.
Ce type de solution permet non seulement de renforcer la communication entre les équipes et la maintenance, mais aussi de simplifier la gestion des tâches quotidiennes.
Avec une GMAO, il est possible d'accéder facilement aux ordres de maintenance de premier niveau, consulter les check-lists quotidiennes, valider les tâches de contrôle réalisées, et signaler rapidement tout dysfonctionnement.
En cas de besoin, les techniciens peuvent générer des demandes d’intervention en quelques clics, assurant ainsi une réactivité optimale et un suivi rigoureux.
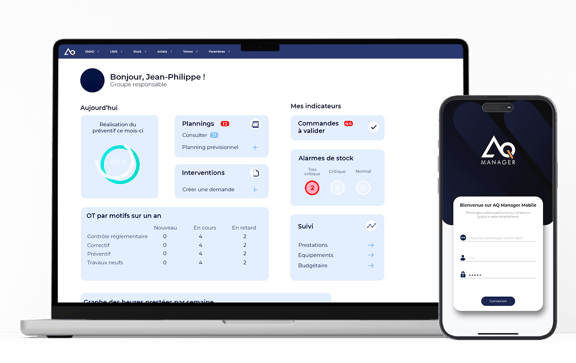
6. Suivi, ajustement et valorisation des résultats
Une fois la stratégie lancée, le suivi devient primordial.
Introduisez des indicateurs de statistiques clés (KPI) spécifiques pour mesurer l’impact : nombre d’inspections effectuées, réduction des pannes, taux de disponibilité des équipements, etc. Ceux-ci sont disponibles dans des tableaux de bord personnalisables au sein du logiciel de GMAO.
Analysez régulièrement ces indicateurs et ajustez les routines si nécessaire. Organisez également des retours d’expérience pour identifier ce qui fonctionne ou non, et pour renforcer leur implication dans le processus.
Enfin, ne sous-estimez pas l’importance de la reconnaissance. Partagez régulièrement les résultats obtenus grâce à cette stratégie. Cette valorisation renforce leur motivation et leur adhésion à la démarche sur le long terme.
La maintenance autonome, ce n’est pas seulement un outil, c’est un changement de cap pour votre entreprise. En impliquant vos opérateurs, vous faites bien plus que prévenir les pannes : vous insufflez une nouvelle culture de responsabilité et d’engagement pour plus d’efficacité.
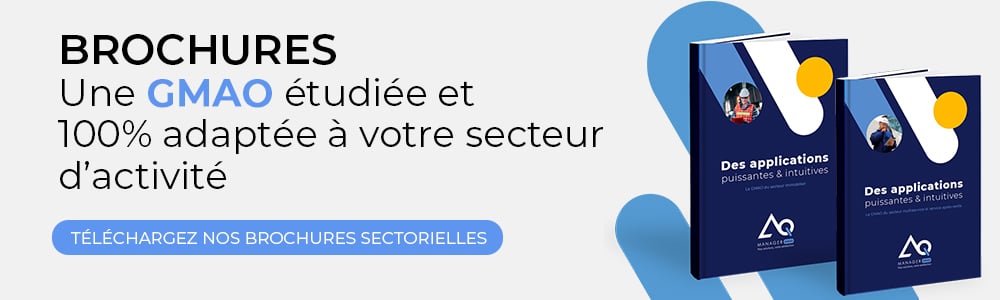