La maintenance préventive, c’est comme les bonnes résolutions : tout le monde y croit, pourtant elle reste trop souvent partielle, incomplète ou reléguée au second plan face aux urgences du quotidien.
Les bénéfices sont néanmoins connus : moins de pannes, moins de stress, plus de disponibilité machine, plus de rentabilité.
Alors pourquoi, sur le terrain, continue-t-on à courir après les urgences, à réparer directement ce qu’on aurait pu éviter ? Pourquoi persiste-t-on à saboter ce levier pourtant stratégique, alors même qu’il pourrait transformer en profondeur la performance industrielle ?
Dans cet article, on ne vous dit pas à quel point la maintenance préventive est une bonne idée.
On vous explique pourquoi elle est si peu appliquée, et ce qui coince vraiment.
Et surtout : par où commencer pour déployer une stratégie de maintenance efficace et réaliste ?
Pourquoi la maintenance préventive est encore sacrifiée face à l'urgence ?
Impossible aujourd’hui de nier l’utilité d’un plan de maintenance préventive. Dans les discours, elle est incontournable : elle réduit les coûts, améliore la durée de vie des équipements, évite les pannes critiques et renforce la sécurité des installations industrielles. C’est presque devenu un réflexe : dans les réunions, les audits ou les présentations stratégiques, la maintenance préventive est sur toutes les lèvres.
Et pourtant, sur le terrain, la réalité est parfois différente. Dans de nombreuses entreprises industrielles, cette stratégie reste cantonnée à des documents théoriques, à de bonnes intentions, mais pas toujours traduites en interventions planifiées.
L’utilisation d’outils tel qu’un logiciel de gestion de maintenance (GMAO) est réelle, mais les machines tournent encore jusqu’à la panne, et les équipes continuent de courir derrière les urgences, dans une logique encore très curative / corrective.
Pourquoi ce grand écart entre la reconnaissance de ses avantages et son application concrète dans les opérations quotidiennes ? Pourquoi une stratégie si essentielle à la performance des équipements et à la sécurité des installations reste-t-elle aussi sous-exploitée ?
Les freins organisationnels et culturels qui bloquent encore son déploiement
Lorsqu’on interroge les équipes du terrain sur les freins à la maintenance préventive, certaines réponses reviennent régulièrement. Ce ne sont pas de mauvaises excuses — elles reflètent souvent des contraintes bien réelles. Mais elles méritent d’être questionnées, car elles peuvent freiner des améliorations importantes.
Parmi celles-ci, il y a :
- Le manque de temps,
- Les plannings chargés,
- Le manque de ressources (humaines ou techniques),
- Les sollicitations constantes des équipes sur d’autres tâches importantes.
Ces remarques doivent être vues comme des signaux. Elles montrent qu’il est peut-être temps de revoir certaines pratiques, de se poser les bonnes questions et d’avancer, pas à pas, vers une stratégie de maintenance plus équilibrée, plus efficace et mieux adaptée aux contraintes du quotidien.
Finalement, ce n’est peut-être pas tant un manque de moyens techniques qui freine l’application réelle de la maintenance préventive. Ni un problème de compétences.
En réalité, le décalage vient souvent d’éléments bien plus profonds, organisationnels et culturels.
La résistance au changement
Premier blocage : la résistance au changement. Derrière le discours d’adhésion, il y a souvent ce réflexe bien ancré : “on a toujours fait comme ça”.
Les techniciens préfèrent s’appuyer sur leur expérience, les responsables privilégient les solutions qu’ils connaissent.
Résultat : la maintenance corrective reste la norme, même si tout le monde sait qu’elle coûte plus cher et expose les machines à des pannes évitables.
De plus, ce frein est renforcé quand la nouvelle technologie mise en place est perçue comme un obstacle plutôt qu’un appui. Pourtant, bien intégrée, une technologie adaptée simplifie les routines et fiabilise les interventions.
La gestion des priorités
Dans beaucoup d’entreprises, la production reste le centre de gravité de toutes les décisions. Quand les ressources sont limitées, la maintenance passe après.
On privilégie parfois le court terme : faire tourner les machines, livrer à l’heure, éviter les retards. Résultat : les opérations de maintenance planifiée sont constamment repoussées ou annulées. On sacrifie la prévention pour répondre à l’urgence.
Il devient alors crucial de repenser l’équilibre entre production immédiate et gestion durable des actifs industriels, en redonnant toute sa place à la prévention dans la stratégie globale.
Le manque de visibilité sur l’état réel des équipements
Sans une analyse structurée des données, difficile de savoir quand intervenir.
Certains responsables s’appuient encore sur l’intuition ou uniquement sur l’historique des pannes. Ce dernier est une base utile - mais insuffisante à elle seule. Elle doit être complétée par des données en temps réel et une vision plus prospective.
Les technologies de maintenance permettent aujourd’hui de surveiller le fonctionnement des actifs, d’anticiper les défaillances et d’optimiser les interventions. Mais ces outils restent souvent mal exploités, ou pire, ignorés.
La culture du dépannage et du court terme
Autre frein majeur : la culture du dépannage. Il arrive que pendant des années, les équipes ont été valorisées pour leur réactivité face aux pannes. Le réflexe reste très curatif : on intervient quand c’est cassé, pas avant.
Changer cet état d’esprit demande une vraie stratégie de maintenance, appuyée par la direction, avec des indicateurs de performance, des plans structurés et une volonté d’inscrire la préventive dans la durée.
À cela s’ajoute une vision trop centrée sur le résultat immédiat très présente dans l’industrie, notamment dans les petites structures. L’objectif immédiat — livrer, produire, tenir les délais — prend parfois le dessus. On investit peu dans la durée de vie des équipements, dans l’entretien systématique, ou dans des pratiques basées sur la condition réelle des machines. Pourtant, les conséquences financières d’un arrêt non planifié ou d’une panne critique sont bien réelles.
Les indicateurs mal alignés avec les objectifs préventifs
Si indicateurs il y a, ils sont parfois mal alignés avec les objectifs de maintenance préventive. On mesure le temps de réaction, mais pas la réduction des arrêts, l’efficacité des interventions planifiées, ou la stabilité du fonctionnement des équipements.
Sans bons repères, difficile de démontrer la valeur de la prévention… et encore plus difficile de la défendre en interne.
La sous-utilisation des outils technologiques
Enfin, les outils eux-mêmes sont parfois mal intégrés. Une GMAO peut être en place, mais sous-utilisée. Les données sont incomplètes, mal renseignées, ou pas exploitables. L’utilisation du logiciel reste superficielle, limitée à la saisie d’ordres de travail sans réelle exploitation des analyses disponibles.
Sans un système fiable pour suivre les interventions, planifier les actions et mesurer les résultats, impossible de piloter efficacement une politique de maintenance.
Le constat est là : ce ne sont pas toujours les outils ou les bonnes intentions qui manquent. C’est la capacité à les ancrer dans les activités quotidiennes, à faire évoluer les habitudes, à structurer le travail des équipes autour d’un plan clair, cohérent, aligné avec les objectifs industriels.
Par où commencer pour déployer une stratégie de maintenance efficace et réaliste ?
Le constat est posé, les freins sont identifiés. Mais alors, par où commencer ? Comment transformer une volonté de faire mieux en une démarche concrète, réaliste et adaptée à vos contraintes terrain ?
Oubliez l’idée qu’il faudrait tout révolutionner du jour au lendemain. Mettre en place une maintenance préventive efficace, c’est une stratégie de progression, pas un grand saut. Ce qui compte, c’est de démarrer avec des actions simples, ciblées et faisables - pour optimiser vos ressources, sécuriser vos installations, et gagner en efficacité dans vos activités quotidiennes.
Un bon point de départ consiste à identifier les avantages attendus pour chaque action engagée : réduction des coûts, baisse du nombre de pannes, allongement de la durée de vie des équipements ou encore amélioration des conditions de travail.
Voici quelques-uns de nos conseils, à intégrer dans un plan de maintenance préventive complet, et à enrichir au fil des priorités et des retours terrain.
1. Utiliser des outils centralisant et rigoureux
Enfin, si ce n'est pas encore le cas, il est important de s’appuyer sur des outils simples mais rigoureux : un logiciel de GMAO configuré par rapport aux réalités du terrain, des checklists digitalisées, des historiques fiables, un suivi structuré des interventions, etc.
Ce type de solution automatisée permet aussi de planifier chaque opération, chaque alerte, chaque incident, de manière systématique. Cette traçabilité est essentielle pour améliorer les performances globales et appuyer vos démarches de qualité ou de certification.
Ce sont ces pratiques, constantes et alignées, qui permettent à la maintenance préventive de sortir du registre des bonnes intentions pour devenir un vrai pilier de la gestion des actifs.
➡️ Découvrez comment un outil de GMAO bien paramétré rend votre maintenance préventive plus simple à piloter.

2. Cartographier les équipements critiques
Commencez par cartographier vos équipements critiques : ceux qui, en cas de défaillance, génèrent le plus de coûts, de pertes de production, ou de risques sécurité.
Sur ces actifs-là, posez les premières briques : fréquence d’entretien, checklists de contrôle, suivi de l’état de fonctionnement, historique des pannes. Vous n’avez pas besoin d’un outil complexe au départ : un tableau structuré ou un logiciel de gestion de maintenance (GMAO) bien configuré suffisent largement à poser les bases et à optimiser l’organisation de vos activités.
3. Impliquer les techniciens dans le processus dès le début
Ensuite, impliquez vos équipes dans la démarche. Les techniciens de maintenance ont une connaissance fine des machines, des dérives, des petits signaux faibles.
Appuyez-vous sur leur expérience pour définir des interventions pertinentes, réalistes et réellement utiles. C’est en valorisant leur regard que vous ferez évoluer les habitudes et que vous passerez d’une logique curative à une logique préventive plus pérenne. Dans toute entreprise, ce changement de posture repose d’abord sur l’adhésion du terrain.
Ne sous-estimez pas les avantages d’une équipe motivée : elle sera plus proactive, plus rigoureuse, et plus apte à repérer les défaillances avant qu’elles ne se transforment en incident majeur.
4. Lister toutes les ressources disponibles
Cette étape requiert une analyse des capacités actuelles de l'équipe : compétences, effectifs, et disponibilité. Il vous faut également évaluer les outils et technologies à disposition, ainsi que les budgets alloués.
Parfois, cela peut mener à reconsidérer les contrats avec les fournisseurs ou à investir dans de nouveaux outils. Le choix du bon logiciel peut ici faire la différence, notamment pour automatiser certaines tâches et structurer l'accès aux données.
La gestion de l'inventaire des pièces détachées est aussi importante pour éviter les retards lors des réparations urgentes. Un stock mal suivi peut provoquer un arrêt complet de la chaîne de production, alors qu’une meilleure planification réduit ces risques.
5. Définir des objectifs de maintenance
Avoir des objectifs clés de gestion de la maintenance peut réduire le recours à la maintenance corrective et contribuer à un programme plus efficient et efficace.
Cela guide également les efforts de l'équipe vers des résultats précis et mesurables pour améliorer l'efficacité et la fiabilité des opérations.
Ils doivent être alignés avec les priorités stratégiques de l'entreprise. On y retrouve, par exemple :
- L'amélioration de l'efficacité opérationnelle,
- L'optimisation des coûts et des budgets,
- La durabilité des équipements,
- La planification des travaux d'entretien,
- La sécurité du personnel,
- La réduction des pannes,
- Etc.
Bon nombre d'entre eux sont fondamentaux pour gérer avec succès l’exploitation d’une installation et peuvent être intégrés pour définir votre propre programme.
6. Utiliser des indicateurs réalistes
Côté pilotage, posez quelques indicateurs simples.
Inutile de surcharger vos Excels ou tableaux de bord : suivez votre taux d’interventions préventives réalisées, le nombre d’arrêts évités, ou encore la disponibilité des équipements concernés. Ce sont ces mesures concrètes qui montrent l’impact de vos actions — et qui donnent envie de continuer. À terme, ces indicateurs vous aident aussi à identifier les défaillances, à renforcer la sécurité, et à ajuster la répartition entre maintenance préventive et curative.
Associer ces indicateurs vous permettra de prioriser les efforts de travail et d’anticiper les points de fragilité dans votre parc d'équipements.
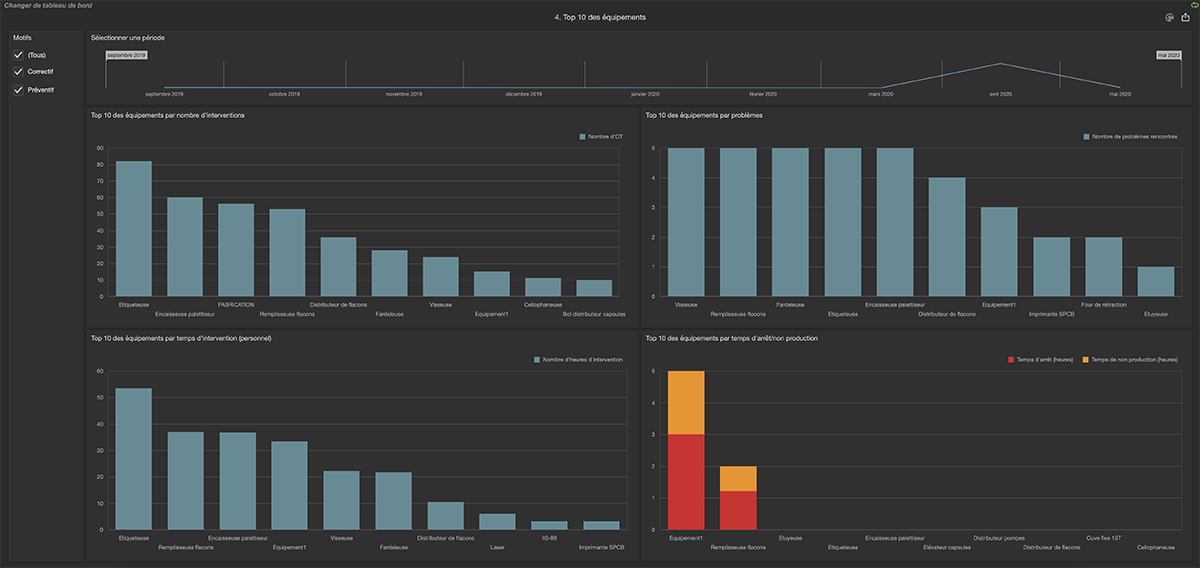
Tableau de bord centralisant les indicateurs de performance des équipements suivis dans la GMAO.
Et surtout, restez cohérent dans le temps. Mieux vaut un plan de maintenance modeste mais respecté qu’un planning ambitieux jamais appliqué. C’est la régularité des petites actions qui construit la fiabilité des installations. Et si certains points ne fonctionnent pas ? Ajustez, testez autre chose, mais ne lâchez pas la logique.
Il n’est jamais trop tard pour structurer sa maintenance. Il n’y a pas de “bon moment”, mais il y a toujours une meilleure façon de faire. Et dans un contexte où les ressources sont parfois limitées, où chaque heure d’arrêt compte, investir du temps dans l’entretien préventif, c’est reprendre le contrôle de ses équipements industriels, de ses coûts, de ses opérations, et de la performance globale de son entreprise.
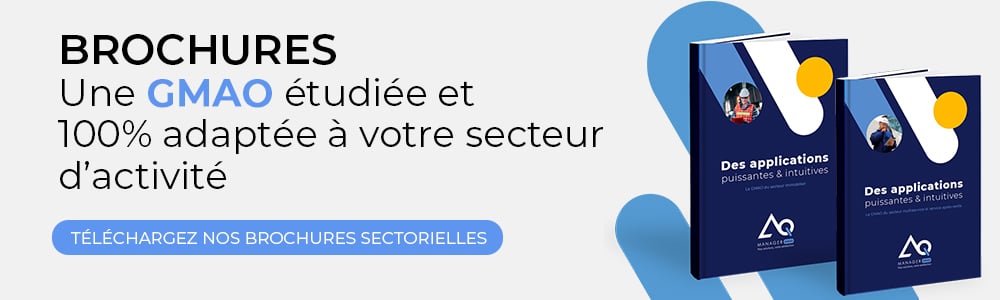