Responsable de maintenance, êtes-vous prêt à transformer les grognements de vos machines en ronronnements harmonieux grâce à un plan de maintenance bien établi ?
Si chaque minute d'arrêt technique sonne comme un euro qui s'envole, c'est le moment de réagir. Entre les coûts d’immobilisation et les interventions en urgence qui mobilisent vos équipes dans le désordre, l’absence de stratégie devient un vrai risque. La mise en place d'un plan de maintenance structuré devient alors une urgence.
Mais attention, ce n'est pas juste une liste de vérifications – c'est une stratégie complète qui assure non seulement le bon fonctionnement de vos équipements mais qui vise aussi un équilibre parfait entre les dépenses et la satisfaction de ceux qui ont les mains dans le cambouis.
Avant de foncer, n'oubliez pas : il y a des étapes préparatoires essentielles à respecter. Sur le terrain, chaque détail compte et brûler les étapes pourrait vous coûter cher.
Découvrez-les sans plus tarder.
Plan de maintenance : qu'est-ce que c'est ?
Avant de parler plan de maintenance, prenons un pas de recul. Car un bon plan n’est jamais le point de départ, mais bien le résultat d’une stratégie réfléchie.
La stratégie, c’est la vision globale. Elle détermine comment vous choisissez de maintenir vos équipements : Allez-vous privilégier la maintenance préventive, conditionnelle, curative ou prédictive ? Quels sont les équipements critiques à surveiller de près ? Quel niveau de risque êtes-vous prêt à accepter ? Quels sont les objectifs ?
Ensuite, il y a la planification, qui traduit la stratégie en actions concrètes. Elle organise les opérations dans le temps en déterminant les équipements à entretenir, la fréquence, les ressources, etc.
Finalement, le plan de maintenance est l'outil qui formalise tout cela.
➡️ Un plan de maintenance est une méthode structurée destinée à prévenir les pannes avant qu'elles ne se produisent, assurant ainsi que vos machines tournent aussi précisément que des horloges suisses, sans les grincements.
L'objectif est donc d'assurer la disponibilité des équipements, limiter les arrêts inopinés et prolonger la durée de vie de vos actifs. Il liste
- Les actions et leur périodicité
- Les équipements concernés
- Les pièces et compétences nécessaires
- Les échéances précises.
Le plan de maintenance s’appuie à la fois sur les exigences réglementaires, les recommandations des fabricants et les constats issus du terrain.
Plan de maintenance vs ordonnancement : quelle différence ?
Le plan de maintenance définit quoi faire, sur quels équipements et à quelle fréquence, tandis que l’ordonnancement organise qui intervient, quand et dans quel ordre, en fonction des ressources et des contraintes du moment.
Comment préparer un plan de maintenance solide en 6 étapes ?
Avant de mettre en place votre plan de maintenance, il est essentiel de poser les bonnes bases. Pourquoi ? Parce qu’un plan efficace ne se résume pas à programmer quelques interventions : il doit être ancré dans la réalité de votre site, adapté à vos équipements, vos équipes, vos moyens, et vos contraintes métier.
Voici une feuille de route des étapes à prendre en compte avant de passer à l’action et de mettre en place votre stratégie.
1. Identification des équipements et de leur criticité
Avant tout, il est nécessaire de comprendre précisément quelles sont les exigences spécifiques de l'installation ou de l'usine.
Vous devez commencer par une analyse complète des équipements et des infrastructures. Cela implique de cataloguer chaque machine et système, en notant leur âge, leur état, leur fréquence d'utilisation, et leur rôle dans le processus de production.
L'identification des équipements critiques, ceux dont la défaillance pourrait entraîner des arrêts de production coûteux ou des risques de sécurité, est primordiale.
Cette évaluation nécessite souvent des inspections physiques détaillées et des discussions avec les opérateurs pour comprendre les défis spécifiques à chaque équipement.
2. Revue des ressources disponibles
Cette étape requiert une analyse des capacités actuelles de l'équipe : compétences, effectifs, et disponibilité.
Il vous faut également évaluer les outils et technologies à disposition, ainsi que les budgets alloués.
Parfois, cela peut mener à reconsidérer les contrats avec les fournisseurs ou à investir dans de nouveaux outils technologiques.
La gestion de l'inventaire des pièces détachées est aussi importante pour éviter les retards lors des réparations urgentes.
3. Collecte et analyse des données d'exploitation et de maintenance existantes
L'exploitation des données historiques permet de déceler des modèles de défaillance et d'usure, ce qui aide à anticiper les besoins futurs en maintenance et à optimiser les cycles de préventif.
Cette analyse peut être soutenue par des logiciels de gestion assistée par ordinateur (GMAO), qui facilitent le suivi des interventions passées et l'analyse des tendances.
4. Évaluation des risques et de la conformité réglementaire
L'évaluation des risques et la conformité réglementaire sont des piliers de la maintenance industrielle. Cette étape cruciale garantit que tous les équipements et procédures respectent non seulement les normes de sécurité les plus strictes mais également les exigences légales spécifiques à votre secteur.
Vous devez procéder à une analyse minutieuse des risques associés à chaque équipement et processus. Cela implique d'identifier les dangers potentiels, d'évaluer la probabilité de leur occurrence, et de déterminer l'impact possible sur la production et la sécurité des travailleurs.
5. Définition des objectifs de maintenance
Les objectifs clés de gestion de la maintenance peuvent réduire le recours à la maintenance corrective et contribuer à un programme de maintenance plus efficient et efficace.
Cela guide également les efforts de l'équipe vers des résultats précis et mesurables pour améliorer l'efficacité et la fiabilité des opérations.
Les objectifs doivent être alignés avec les priorités stratégiques de l'entreprise. On y retrouve, par exemple :
- L'amélioration de l'efficacité opérationnelle,
- L'optimisation des coûts et des budgets,
- La durabilité des équipements,
- La planification des travaux d'entretien,
- La sécurité du personnel,
- La réduction des pannes,
- Etc.
Bon nombre de ces objectifs sont fondamentaux pour gérer avec succès l’exploitation d’une installation et peuvent être intégrés pour définir votre propre programme.
6. Établissement d'un dialogue continu avec les opérateurs et techniciens
La communication régulière avec le personnel opérationnel est indispensable pour saisir des retours d'expérience qui échappent parfois aux analyses de données et aux inspections routinières.
Les techniciens, par leur expérience quotidienne, peuvent révéler des comportements inattendus des machines ou suggérer des améliorations pratiques. Encourager cette communication ouverte contribue non seulement à renforcer une culture de responsabilité et d'innovation continue, mais enrichit également le milieu de travail.
D'un point de vue plus humain, échanger régulièrement avec ses équipes est fondamental. Cela fortifie le moral, booste l'engagement et enrichit la collaboration, assurant ainsi que chaque membre se sente valorisé et pleinement engagé dans les missions communes du laboratoire.
Une fois que vous avez exploré les étapes essentielles pour établir une stratégie solide, il est crucial de réfléchir aux outils qui vous aideront à concrétiser et à optimiser cette stratégie.
À ce stade, l’intégration d’un logiciel de gestion de maintenance assistée par ordinateur (GMAO) prend tout son sens.
Le logiciel de GMAO : un outil stratégique pour le plan de maintenance
Vous le connaissez probablement : le logiciel de gestion de maintenance, dites GMAO, permet de planifier, suivre et d’analyser vos opérations de maintenance.
Il est particulièrement efficace pour l’élaboration d’une approche plus structurée de vos activités. En effet, sa première force réside dans sa capacité à centraliser les informations.
Dès son intégration, le logiciel offre une vision claire et détaillée de l'ensemble des équipements et infrastructures, permettant ainsi d'évaluer l'état actuel et les besoins spécifiques de chaque actif.
Cependant, certaines questions se posent parfois lors de la mise en place d’un système aussi intégratif et central :
❓ Ai-je absolument besoin d’un logiciel de GMAO pour mettre en place un plan de maintenance ?
❓ Si l’intégration du logiciel fait partie de mes plans futurs, dois-je attendre d'avoir un plan bien établi avant de commencer à utiliser la GMAO, ou est-il préférable de commencer immédiatement avec le logiciel pour structurer mes opérations dès le début ?
Planifier avant ou après l'Implémentation de la GMAO ?
De l’œuf ou la poule, lequel est arrivé en premier ? Du plan de maintenance ou de la GMAO, lequel faut-il mettre en place en premier ?
Nous avons identifié deux cas de figure :
1. Implémenter un logiciel de GMAO avant de développer un plan de maintenance complet
✅ Avantages :
- Collecte et analyse des données : Un logiciel de GMAO peut aider à collecter des données opérationnelles dès le début, offrant une base de données riche pour informer le développement du protocole.
- Structure et processus : L'utilisation « précoce » d'un logiciel de GMAO peut aider à structurer les processus dès le départ, intégrant des pratiques comme le préventif et la gestion des ordres de travail, même si le plan n'est pas entièrement défini.
- Adaptation progressive : Le logiciel peut être utilisé pour adapter et affiner cette nouvelle organisation au fil du temps, à mesure que de nouvelles informations sur les équipements et leur performance deviennent disponibles.
🔴 Inconvénients :
- Manque de direction stratégique initiale : Sans un plan de maintenance clairement défini, l'utilisation du logiciel peut être moins ciblée, ce qui peut entraîner des inefficacités initiales ou une sous-utilisation des fonctionnalités du logiciel.
2. Développer un plan de maintenance avant d'implémenter un logiciel de GMAO
✅ Avantages :
- Direction et objectifs clairs : Avec un plan de maintenance déjà en place, l'implémentation d'un logiciel de GMAO peut être plus ciblée et alignée avec les objectifs stratégiques déjà déterminés.
- Optimisation des fonctionnalités : Le plan de maintenance peut aider à identifier les fonctionnalités spécifiques du logiciel de GMAO qui seront les plus utiles, permettant une personnalisation et une intégration plus efficaces.
🔴 Inconvénients :
- Risques d'ajustement post-intégration : Si le plan de maintenance n'est pas flexible, l'introduction ultérieure d'un logiciel de GMAO peut nécessiter des ajustements significatifs du plan pour tirer pleinement parti des capacités technologiques offertes.
L'ordre d'implémentation d'un logiciel de GMAO et du développement d'un plan de maintenance soulève une question stratégique cruciale pour les organisations souhaitant maximiser l'efficacité de leurs opérations.
La décision dépendra finalement des besoins spécifiques de votre entreprise, de sa capacité à s'adapter et de la nature de ses opérations.
Une approche hybride, débutant avec un cadre de maintenance basique avant l'introduction de la GMAO, pourrait aussi être envisagée pour équilibrer les avantages des deux méthodes.
➡️ Vous souhaitez en savoir plus sur les logiciels de gestion de maintenance ? Bénéficiez d'une démo personnalisée auprès de nos experts !

Les bénéfices sur le long terme du plan de maintenance
Jetons un œil aux bénéfices, où les coûts ne font pas qu'un simple passage éclair mais décident de s'installer confortablement pour le long terme :
- Réduction des coûts de maintenance et d’exploitation,
- Amélioration de la fiabilité et de la disponibilité des équipements,
- Conformité réglementaire et sécurité améliorée,
- Augmentation de l’efficacité opérationnelle,
- Prévisibilité financière et budgétisation améliorée,
- Durée de vie prolongée des actifs,
- Amélioration de la culture d’entreprise et de la satisfaction des employés.
En résumé, élaborer un plan de maintenance robuste n'est pas un luxe, mais une impérieuse nécessité dans le monde industriel actuel, où chaque minute d'arrêt machine peut coûter cher.
Au-delà de la simple prévention des pannes, un système structuré est un pilier essentiel pour équilibrer efficacement performance, coûts et satisfaction des équipes.
Adopter une démarche proactive en suivant les étapes clés avant de déployer votre stratégie, comme l'analyse des besoins, la revue des ressources, et l'implémentation de technologies comme la GMAO, transforme non seulement les défis quotidiens en opportunités, mais forge également une compétitivité durable.
N'attendez pas que les coûts d'urgence et les pannes dictent votre calendrier ; prenez les devants pour une tranquillité industrielle assurée et une efficacité accrue.
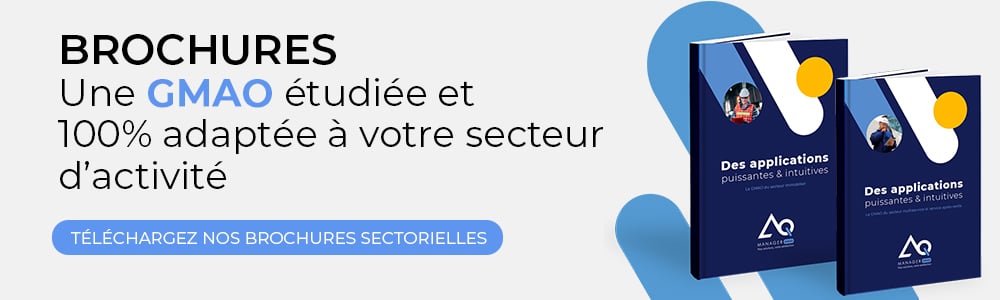